Thermal Regulation Strategies for Extended Tooling Component Service Life
Understanding Thermal Stress in Tooling Components
Impact of Overheating on Component Longevity
High temperatures significantly impact the longevity of tooling components by causing thermal fatigue, a phenomenon where repeated thermal cycling leads to material degradation. Studies indicate that components exposed to excessive heat tend to wear out faster, ultimately affecting their performance and reliability. This wear occurs as overheating accelerates various deterioration mechanisms, including oxidation and material microcracking. To combat this, regular monitoring of temperatures is essential. By maintaining consistent checks, businesses can effectively predict when components may start to degrade and take preventive action, thus extending their lifespan and ensuring steady operational performance.
Common Failure Points in Leather Die Presses and Strip Cutters
Leather die presses and leather strip cutters often fail at specific points, primarily at joints or areas with inadequate heat dissipation due to thermal stress. Industries using these machines must understand which parts are most prone to these stresses, as it can significantly aid in predictive maintenance. According to research, components situated in high-stress areas tend to fail faster because of the constant expansion and contraction they endure during thermal cycling. Understanding the thermal stress weaknesses in a leather die press or strip cutter can reduce downtime and maintenance costs, and lead to an overall more efficient production process.
Core Thermal Regulation Strategies for Tooling Systems
Heat Sinking and Conduction Optimization
Effective thermal regulation is essential for extending the lifespan of tooling components, and heat sinking plays a pivotal role in this process. Using advanced heat sinking materials can significantly lower the temperature of tooling components, thereby enhancing their durability. Moreover, optimizing thermal conduction is crucial for minimizing energy loss during operations, which results in improved efficiency. Reports from the industry indicate that employing effective heat sinking strategies can lead to a component lifespan improvement of up to 30%. This highlights the substantial impact that proper heat management can have on tooling efficiency, particularly in high-stress environments.
Coolant Systems for Friction Reduction
Advanced coolant systems are critical in reducing friction during tooling operations, directly enhancing performance. By selecting the appropriate coolant type, businesses can improve thermal management, especially in high-temperature scenarios, leading to smoother operations. Data from various studies suggest that machinery equipped with optimized coolant systems can experience up to 25% fewer failures. This reduction in failure rates not only prolongs equipment life but also bolsters overall productivity, making the implementation of effective coolant systems a sound investment for industries reliant on high-volume tooling processes.
Thermal Barrier Coatings for High-Tolerance Applications
In high-tolerance applications, thermal barrier coatings serve as a crucial protective layer for tooling components against extreme temperature fluctuations. These coatings not only provide excellent insulation but also enhance wear resistance, contributing to longer tool life. Research supports their effectiveness, demonstrating that thermal barrier coatings can maintain operational integrity even under the most challenging conditions. By incorporating these coatings, industries can ensure that their tooling systems remain robust and reliable, leading to consistent performance and reduced downtime, ultimately optimizing productivity.
TengHong Machinery’s Advanced Thermal Solutions
TH-141C Horizontal Dyeing Machine: Precision Cooling for Curved Edges
The TH-141C Horizontal Dyeing Machine stands out with its precision cooling technology, making it ideal for intricate dyeing applications involving curved edges. This advanced machine has been engineered to maximize thermal management, ensuring consistent color application and maintaining the integrity of delicate materials. Users have consistently praised this model for its operational efficiency, as evidenced by testimonials indicating fewer thermal-related failures. Such feedback underscores the TH-141C's capability to deliver consistent performance in handling complex dyeing tasks.
.png)
TH-630 Bilateral Dyeing System: Synchronized Thermal Control
The TH-630 Bilateral Dyeing System incorporates synchronized thermal control, which significantly enhances dye application uniformity. By leveraging advanced sensors, this system maintains optimal temperatures across both sides of the material, effectively preventing uneven dyeing and material stress. Case studies have demonstrated that this precise temperature regulation enhances product quality while reducing waste. Such innovations highlight the importance of thermal management in maintaining high production standards and efficiency in dyeing processes.
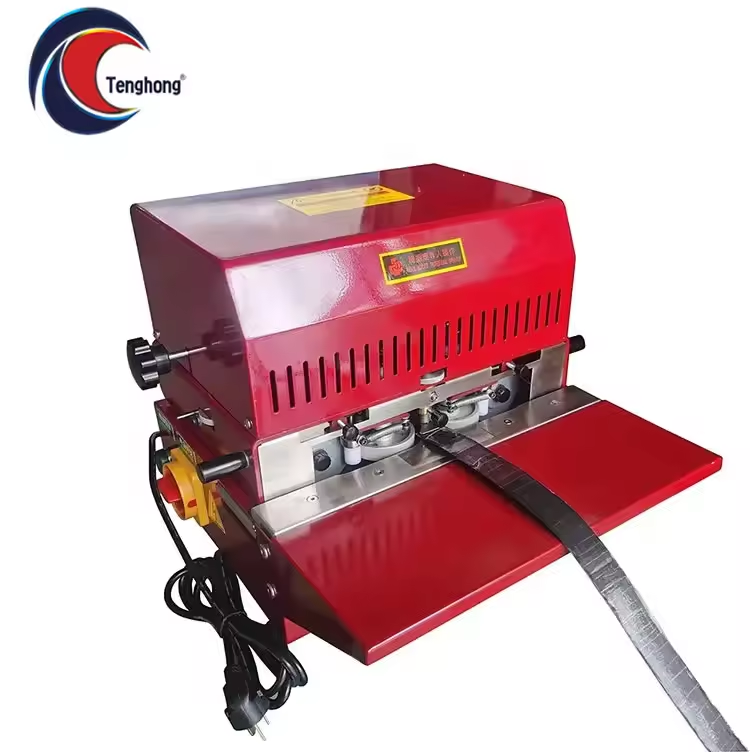
TH-226 Hydraulic Cutter: Heat-Resistant Hydraulic Efficiency
The TH-226 Hydraulic Cutter is renowned for its heat-resistant components, which sustain hydraulic performance under demanding conditions. Designed to manage thermal stress, this machine ensures an extended operational lifespan and steadfast reliability. Technical evaluations reinforce its superior thermal design, citing a notable decrease in maintenance needs and a boost in productivity. Its engineering showcases the emphasis TengHong places on integrating heat-resistant technologies to elevate machine efficiency and longevity.
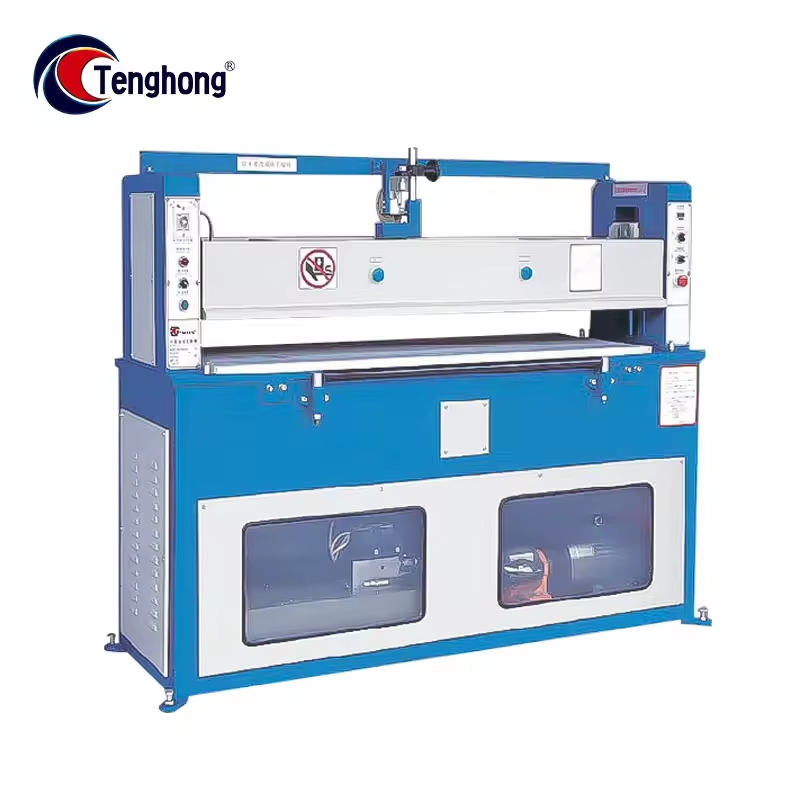
Material Selection and Maintenance for Thermal Durability
High-Thermal-Conductivity Alloys in Shoe Stitching Machines
Using high-thermal-conductivity alloys in the construction of shoe stitching machines can significantly enhance their performance. These materials enable better heat management, ensuring increased operational stability and efficiency. By improving thermal management, sewing machines can handle high-speed operations without overheating, maintaining consistent stitching quality. Expert analyses show that machines incorporating these alloys frequently operate at higher efficiency levels. As a result, these enhancements lead to a prolonged lifespan for the machinery, indicative of lower maintenance costs and better return on investment.
Preventive Maintenance for Consistent Thermal Performance
Regular preventive maintenance is crucial in tooling machinery to maintain optimal thermal performance and avoid unexpected breakdowns. By conducting proactive checks and adjustments, potential issues can be identified and resolved before they lead to critical failures. Organizations that implement routine maintenance programs report up to a 40% decrease in unexpected machinery failures. This practice not only ensures consistent thermal regulation but also extends the machinery's operational life and effectiveness, safeguarding the business against unnecessary downtime and repair costs.