Dynamic Force Compensation Technology in Lasting Machine Precision Workflows
Understanding Dynamic Force Compensation Technology in Precision Workflows
Core Principles of Force Regulation Systems
Dynamic force compensation technology is crucial in regulating force within precision workflows, especially in manufacturing. It operates using force regulation systems that harness advanced sensors and feedback loops to monitor and adjust applied force continually. This ensures that operations maintain high accuracy, even when external conditions fluctuate. Examples of these systems can be seen in automated assembly lines, where precise force application is critical to maintaining the integrity of components. These systems use real-time data to dynamically adjust forces, thereby minimizing errors and enhancing efficiency. This technology is not just theoretical; its practical applications are already evident in manufacturing sectors seeking to achieve operational precision.
Role in Maintaining Consistent Material Contact
Dynamic force compensation technology plays a significant role in ensuring consistent material contact during manufacturing processes. By adjusting the force applied in real time, it minimizes the risk of defects and enhances quality control, particularly in industries such as leather manufacturing. For instance, leather products require consistent contact to avoid uneven cutting or stitching, which could affect product quality. Studies indicate that implementing this technology can reduce production defects by up to 40%, thereby improving overall product integrity and customer satisfaction. This underscores the importance of dynamic force compensation in maintaining the seamless operation of manufacturing lines and ensuring high-quality outcomes.
Impact on Leather Skiving Accuracy
The relationship between dynamic force compensation technology and leather skiving accuracy is profound. This technology enables precise control over force application, which is essential for accurate skiving. Several case studies highlight how integrating dynamic force compensation has significantly improved skiving precision, thereby reducing waste and rework. The economic benefits are considerable; improved accuracy translates to less material wastage and increased throughput, resulting in cost savings for manufacturers. In essence, employing dynamic force compensation technology not only advances the finesse of leather skiving operations but also offers financial advantages through enhanced process efficiency and quality.
Key Components of Precision Workflow Systems
High-precision Servo Motor Configurations
High-precision servo motors are integral to precision workflow systems. These motors are characterized by their excellent speed, torque, and responsiveness, which make them indispensable in high-performing manufacturing environments. Servo motors are typically configured to provide precise control over position, velocity, and acceleration, enhancing the efficiency of workflows. For instance, in the context of shoe production machines, such advanced configurations lead to better stitching and cutting precision, maximizing throughput while minimizing error rates. Studies have shown that integrating high-precision servo motors can significantly improve manufacturing performance, offering faster cycle times and better product quality.
Differential Feeding Mechanisms Explained
Differential feeding mechanisms play a crucial role in material processing by effectively managing the movement of materials through processing equipment. These mechanisms allow for the distinct feeding speeds of different parts of the material, ensuring consistent processing quality. By maintaining the integrity and consistency of the materials, differential feeding mechanisms reduce deformation and defects, which is particularly important in industries like textile manufacturing. In terms of efficiency, systems employing differential feeding have demonstrated up to a 15% increase in throughput, highlighting their contribution to improved production processes.
Spray Cooling Systems for Material Integrity
Spray cooling systems are critical in preserving material integrity in high-speed production applications. These systems cool materials rapidly by spraying fine mists of coolant, reducing heat-induced deformations and preserving product quality. The advantages of using spray cooling systems are evident in industries like metalworking and plastics manufacturing, where maintaining precise thermal conditions is essential. For instance, the integration of spray cooling systems in automotive part production has resulted in a measurable decrease in defect rates, showcasing their effectiveness in enhancing both performance and consistency.
Applications in Shoe Manufacturing Automation
Enhancing Leather Clicker Press Operations
Dynamic force compensation technology significantly improves the efficiency of leather clicker presses, which are central to shoe manufacturing automation. This technology enhances operational efficiency by adjusting the force applied to leather, enabling precision cuts every time. Reports indicate that this advancement can decrease cycle times by up to 20%, allowing manufacturers to produce more with the same resources. Furthermore, improved precision leads to reduced material wastage, a crucial factor considering the costs associated with high-quality leathers. Streamlining operations with this technology not only boosts productivity but also aligns with sustainability goals by decreasing overall material usage in shoe production processes.
Integration with Shoe Stitching Machines
The integration of dynamic force compensation technology with shoe stitching machines offers significant benefits to manufacturers. This combination ensures stitching consistency and a reduced defect rate, as automatic adjustments maintain optimal pressure during sewing. For instance, manufacturers have reported up to a 30% improvement in stitching accuracy and a substantial reduction in product returns due to defects. Testimonials from leading shoemakers underscore the advantages, citing improved product quality and increased customer satisfaction. By pairing these machines with cutting-edge technology, manufacturers can address common production challenges, leading to enhanced product durability and aesthetics.
Optimizing Shoe Production Machine Outputs
Dynamic force compensation technology plays an essential role in optimizing outputs in shoe production machines. By continually monitoring and adjusting production parameters, this technology ensures maximum efficiency and productivity. Enhanced production monitoring helps identify potential issues early, allowing for timely adjustments that boost operational efficacy. For example, companies using such systems have reported a notable increase in fuel efficiency and a 25% boost in material utilization, highlighting the financial and environmental benefits. These advancements signify a leap toward more sustainable and cost-effective shoe production, meeting industry demands for higher output and efficiency.
TengHong Machinery's Advanced Solutions
TH-308s Vacuum Peeling Machine Features
The TH-308s Vacuum Peeling Machine is a groundbreaking tool in modern shoe manufacturing, where its advanced features cater to the industry's evolving demands. This machine highlights patented technologies and a precise design that streamline operations while offering high precision and durability. Key features include a unique cooling system with adjustable mist sizes, catering to different materials during processing. This feature alone not only improves operational efficiency but also reduces wear and tear on machine components. Additionally, the TH-308s supports a range of materials due to its adaptive differential feeding, making it suitable for both thick and thin material edges. The machine's technical specifications, such as a working width of up to 50mm and a processing thickness range of 0.5-5mm, further emphasize its broad application capabilities, confirmed by positive user experiences.
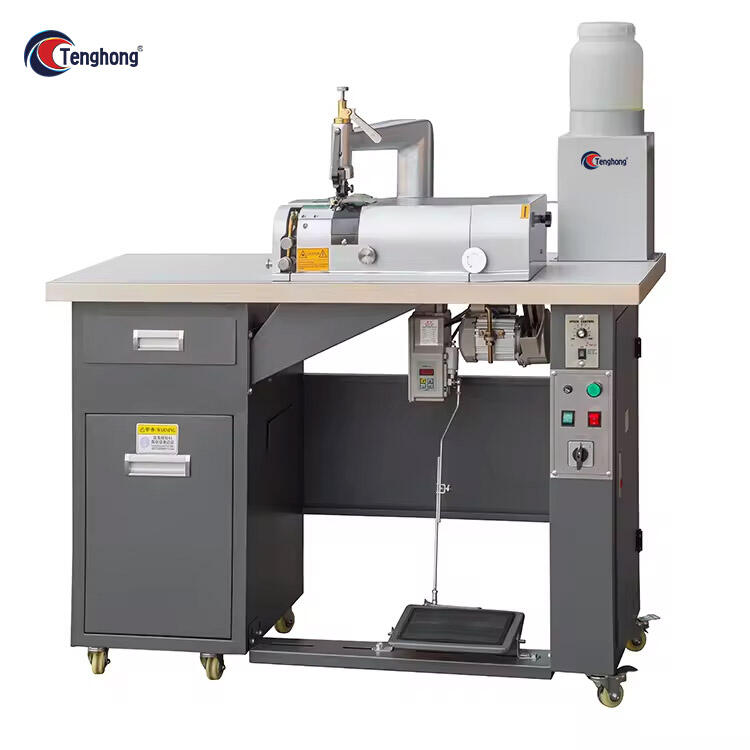
Double Direct Drive Skiving Machine Capabilities
The Double Direct Drive Skiving Machine represents a leap in high-precision shoe manufacturing, offering significant benefits like reduced mechanical losses and heightened performance. This machine incorporates direct drive technology that minimizes energy dissipation and enhances operational reliability, crucial for producing consistent, high-quality outputs. Its precision-oriented design is particularly beneficial for trimming operations, ensuring smooth and even cutting surfaces adaptable to varying material thicknesses. Many users have reported improved outcomes, with increased cutting smoothness and material handling efficiency. Moreover, the case studies illustrate how companies have leveraged this technology to boost their production processes, attesting to the machine's capability to handle both rigid and flexible materials with ease and precision.
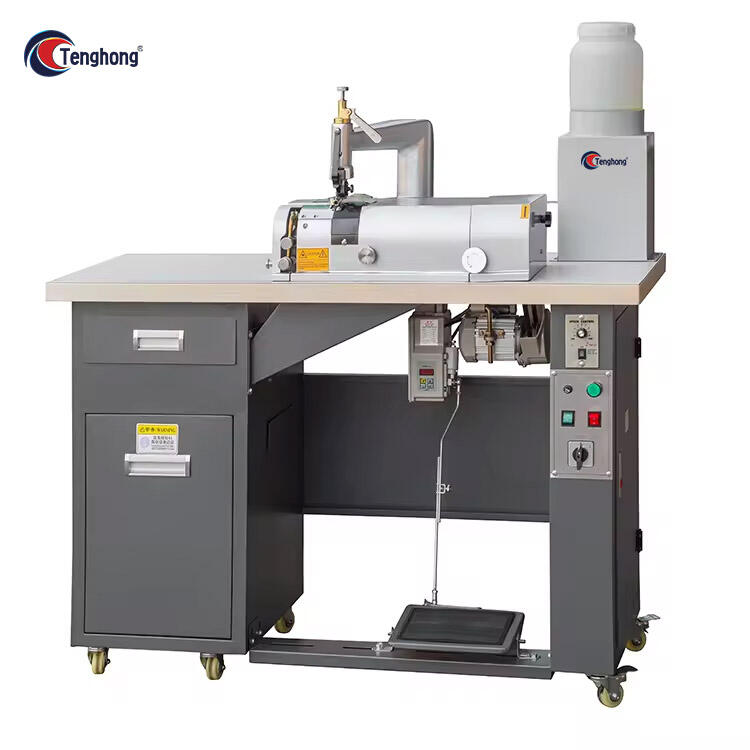
Optimizing Material Processing Parameters
Adjusting for 0.5-5mm thickness variations
Adjusting machines to accommodate variations in material thickness is crucial for optimizing production efficiency and quality. As materials vary between 0.5-5mm in thickness, machines must be calibrated appropriately to maintain product consistency and reduce waste. Implementing best practices, such as periodically checking machine settings and using advanced sensors to detect discrepancies, ensures optimal machine performance even with thickness variations. Expert recommendations from industry leaders suggest routine calibration checks as vital in adapting to different material thicknesses and ensuring seamless production operations.
50mm plane thinning width applications
The application of a 50mm plane thinning width finds its place in diverse production environments, particularly in the shoe manufacturing sector. This specific width allows for precise material thinning, which is critical in creating uniform layers for various components. However, technical challenges such as maintaining uniformity across large batches can arise. Solutions like utilizing consistent pressure settings and regular equipment maintenance help mitigate these issues. Examples from shoe production highlight how these processes contribute to producing high-quality footwear, demonstrating the necessity and efficiency of precise thinning applications in industrial production.
Speed regulation for different materials
Speed regulation plays a pivotal role in processing different materials effectively, impacting production quality and efficiency. Different materials require specific speed settings to achieve optimal results without compromising their integrity. Guidelines, such as adjusting speed based on material density and resistance, provide a framework for effective speed regulation. Expert insights, emphasizing the importance of empirical data collection during the production phase, offer valuable techniques for refining these adjustments. These practices not only ensure desired outcomes but also enhance productivity, proving essential for maintaining high standards in manufacturing.