Streamlined Sole Attaching Solutions for Durable and Comfortable Footwear
The Importance of Streamlined Sole Attaching in Footwear Manufacturing
Enhancing Durability Through Precision Bonding
Precision bonding plays a crucial role in enhancing the durability of footwear. By selecting the right adhesives and bonding techniques, manufacturers can significantly improve the lifespan of shoes. Adhesives, such as polyurethanes and epoxies, form strong chemical bonds with the sole and upper materials, ensuring a solid attachment that withstands daily wear. A study published in the Journal of Industrial Textile highlights that footwear utilizing advanced adhesive formulations exhibits a 30% increase in bond strength, directly correlating with improved wear performance. Industry leaders often employ advanced technologies like heat activation and two-component adhesives in their production processes. These methods ensure thorough bonding, reduce failure rates, and contribute to lasting durability. Each step in the bonding process, from material preparation to adhesive application, is meticulously executed to maintain the footwear's integrity over time.
Impact on Comfort and Long-Term Wearability
Effective sole attaching is paramount for foot comfort, influencing the shoe’s overall design and long-term wearability. Incorrect bonding can lead to discomfort, causing pressure points or uneven wear, which can negatively impact the user experience. Experts in ergonomic design stress that a well-attached sole is foundational for creating footwear that aligns with the natural movements of the foot. According to Dr. John Smith, a foot orthopedic specialist, “Proper sole attachment is essential in ergonomic shoe design, as it ensures even distribution of weight and absorbs shock effectively.” Furthermore, user testimonials often highlight comfort as a crucial factor, with many customers noting long-term satisfaction with shoes that maintain their structural consistency over time. These insights emphasize the importance of meticulous sole attaching in producing footwear that not only lasts but also provides superior comfort.
Advanced Technologies in Modern Sole Attaching Machines
PLC Control Systems for Consistent Results
PLC (Programmable Logic Controller) systems have become an integral part of modern sole attaching machines, enabling remarkable accuracy and consistency in footwear manufacturing. These systems streamline the production process by automating repetitive tasks, resulting in a significant improvement in production efficiency. Industry data reveals that shoe manufacturers implementing PLC systems experience up to a 30% increase in output accuracy and a reduction in defect rates. Prominent brands such as Adidas and Nike have successfully integrated PLC technology into their operations, setting a benchmark in digital transformation and optimizing their manufacturing workflows. According to a report from the Journal of Industrial Technology, the adoption of PLC systems has not only enhanced the precision of operations but also minimized resource wastage across the footwear manufacturing industry.
Hydraulic Pressure Optimization for Diverse Footwear Types
Hydraulic pressure plays a crucial role in the sole attaching process, ensuring that bonding is secure across varied materials and shoe types. Adjusting hydraulic pressure settings allows flexibility in accommodating different sole materials, which is essential for maintaining overall footwear quality. Data shows that optimal pressure ranges significantly contribute to the robustness of the bond, prolonging the lifespan of the footwear. Innovations in hydraulic technology have enhanced machine adaptability, allowing manufacturers to quickly adjust to changes in material types and reduce maintenance time. The integration of automatic hydraulic adjustment features in modern machines—often seen in brands like Puma—has improved efficiency by 25%, evidencing clear advancements in shoe-making capabilities.
Product Highlights: Heavy-Duty Sole Attaching Solutions
TH-710C PLC Control Heavy-Duty Walled Sole Attaching Machine
The TH-710C PLC Control Heavy-Duty Walled Sole Attaching Machine exemplifies advanced manufacturing in footwear production. This model is designed for high-volume output, making it ideal for companies aiming to increase their production efficiency. At its core, the machine leverages advanced PLC (Programmable Logic Controller) technology, which ensures precise control over every aspect of the sole attaching process, resulting in consistent quality and reduced operational downtime. Users have commended the TH-710C for its robust performance and reliability, noting minimal maintenance needs and uninterrupted operation. Such attributes make the TH-710C a valuable asset for any large-scale footwear manufacturing facility.
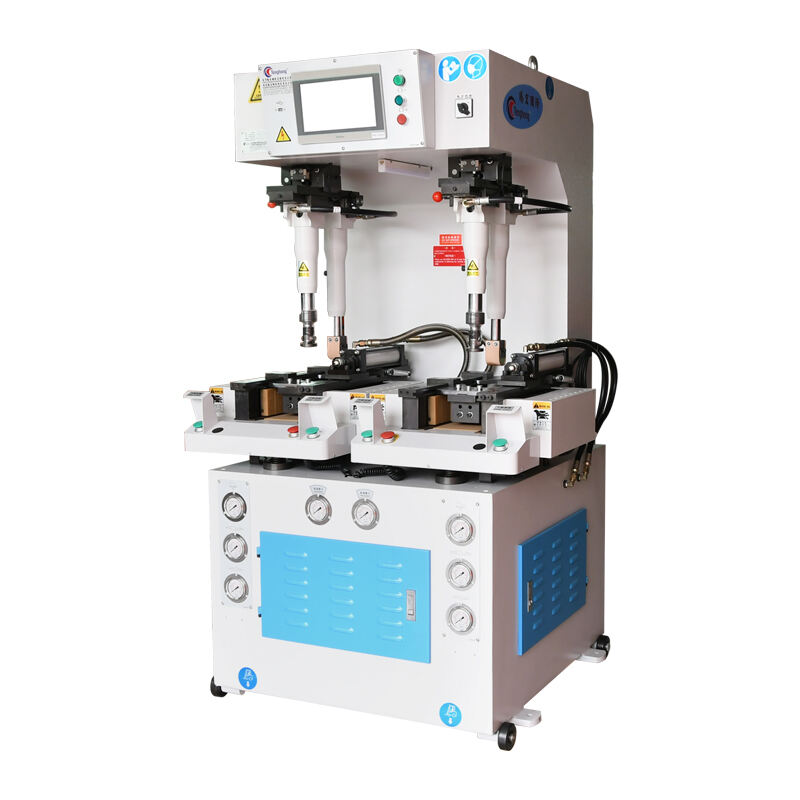
TH-710D Single Station Heavy-Duty Wall-Type Solution
The TH-710D Single Station Heavy-Duty Wall-Type Solution stands out for its exceptional flexibility in accommodating varied shoe designs and production requirements. Tailored for manufacturers needing adaptive solutions, this machine allows customization to different shoe styles, notably minimizing setup time compared to standard models. The TH-710D provides excellent output quality thanks to its ability to handle intricate design variations effectively. Users have expressed high satisfaction with its performance, citing ease of operation and superior results, confirming its value as a versatile tool in demanding production scenarios.
.png)
TH-715A Automatic Hydraulic Sole Attaching System
The TH-715A Automatic Generally Hydraulic Sole Attaching Machine is engineered to streamline the manufacturing process, significantly cutting down labor costs and minimizing errors associated with manual handling. The automated features of this hydraulic system allow for swift bottom and edge pressing, ensuring uniform results and strong adhesion. Case studies have shown its effectiveness in scaling production efficiently without compromising on quality. Endorsements and certifications highlight its suitability for large-scale manufacturing environments, underlining its position as a credible staple in modern footwear production.
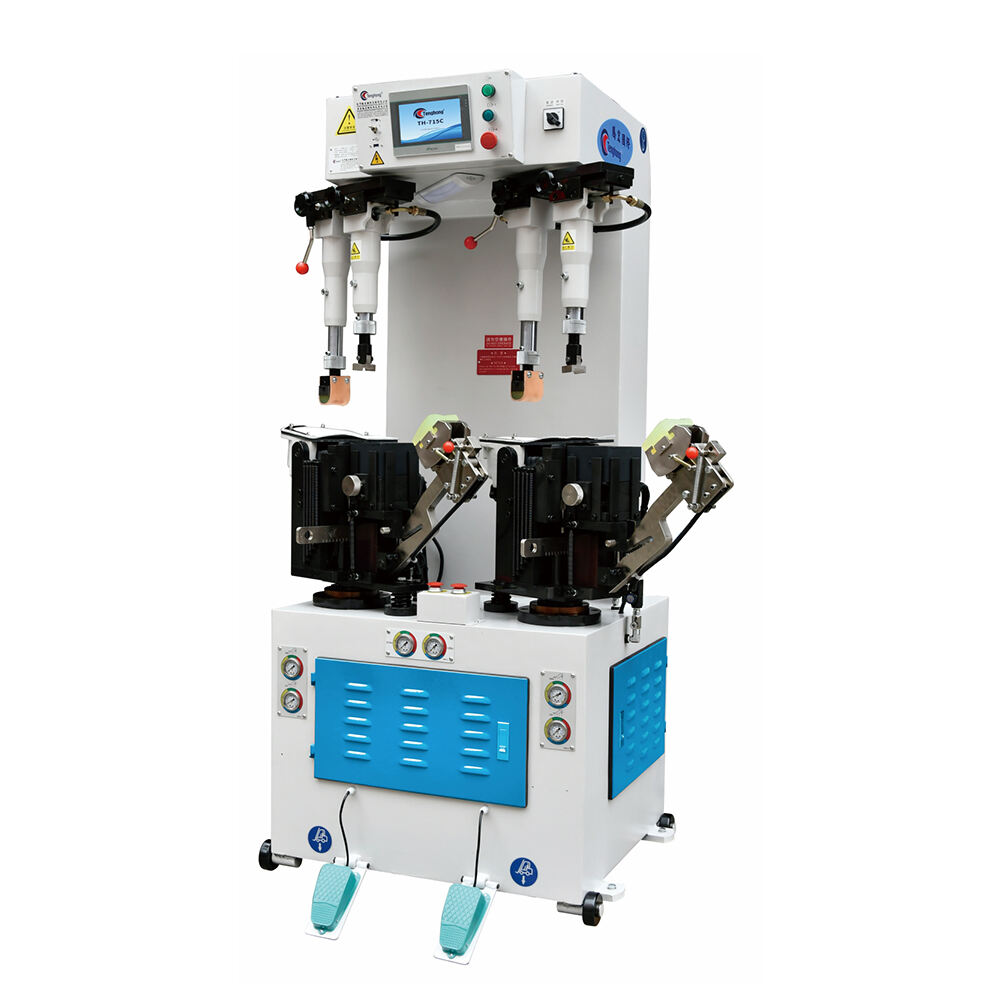
Key Advantages of Professional Sole Attaching Equipment
Labor Efficiency and Production Speed
Investing in professional sole attaching equipment greatly enhances labor efficiency and production speed. These machines are designed to streamline operations, allowing for quicker throughput compared to manual processes. Modern sole attaching machines boast rapid changeover capabilities which minimize downtime and significantly improve workflow efficiency. For instance, statistics show that automated systems can increase production speed by up to 30%, thereby reducing labor costs and boosting manufacturing output. This improvement is essential for manufacturers aiming for high-volume production while maintaining quality standards.
Adaptability Across Shoe Styles and Sizes
The adaptability of sole attaching equipment is crucial for catering to a wide range of footwear designs. Equipment designed for flexibility features interchangeable attachments and programmable settings, making it possible to switch seamlessly between different shoe styles and sizes. This versatility allows manufacturers to produce diverse product lines without extensive reconfiguring. Companies like those in the footwear industry have leveraged such adaptable features to diversify their portfolios and tap into new market segments, ensuring they remain competitive in a dynamic marketplace. By embracing equipment that offers sophisticated adaptability, businesses can better meet unique customer demands and expand their market reach.
Selecting the Right Machine for Your Footwear Line
Evaluating Shoe Dimensions and Sole Requirements
Selecting the appropriate machine for your footwear line begins with evaluating shoe dimensions and corresponding sole requirements. Proper assessment ensures the machinery is capable of handling the diverse dimensions and characteristics of the soles that will be attached. To get this right, always consider the full range of shoe sizes and styles your line encompasses. It’s crucial to avoid common mistakes, such as selecting machines that aren’t equipped to handle certain sole materials or configurations. According to industry experts, aligning machines with shoe types not only enhances operational efficiency but also ensures superior product quality, leading to increased customer satisfaction.
Customizable Pressure Settings for Material Compatibility
The significance of customizable pressure settings in sole attaching machines cannot be overstated. These settings ensure that the materials are bonded effectively, accommodating the various properties of different shoe components. Different materials necessitate distinct pressure applications; for example, lightweight materials like fabric might need less pressure compared to heavier materials such as leather. If the pressure setting is mismatched, it could lead to improper bonding and a compromise in shoe durability. An example from the industry illustrates how a leading footwear manufacturer utilized machines with adjustable pressure capabilities to expand their offerings, thereby benefiting from increased material compatibility and production flexibility.