Energy Recovery Systems in Hydraulic Shoemaking Equipment Operation
Reducing Energy Waste in Leather Clicker Press Operations
Hydraulic energy recovery systems play a crucial role in minimizing energy wastage during operations in leather clicker presses. These systems effectively reclaim energy that would otherwise be lost, significantly enhancing the efficiency of manufacturing processes. According to a study by the International Energy Agency, it is possible to reclaim up to 30% of operational energy with the use of these systems, resulting in notable cost reductions for manufacturers. Implementing hydraulic energy recovery not only supports sustainable practices but also boosts the bottom line for businesses involved in leather production.
Integration with Shoe Stitching Machine Workflows
When integrated with shoe stitching machines, hydraulic energy recovery systems support a seamless and efficient workflow. These systems deliver a stable power supply, reducing dependency on external energy sources, thereby optimizing the overall efficiency of production lines. As experts suggest, compatibility with existing systems is essential for harnessing maximum efficiency. By ensuring that hydraulic energy systems work in tandem with shoe stitching machines, businesses can streamline operations and reduce energy costs, contributing to a more sustainable manufacturing process.
Pressure Reclamation in Leather Die Press Applications
In leather die press applications, hydraulic energy recovery systems offer significant benefits by reclaiming pressurized fluid for reuse. This process enhances the overall efficiency of the system, allowing for better management of hydraulic resources. Statistics indicate that pressure reclamation can reduce operational pressures by 25%, which helps in optimizing performance and conserving energy. By focusing on pressure reclamation, manufacturers can improve the durability and efficiency of their leather die press systems, aligning with the broader goals of sustainability and resource efficiency in the shoemaking industry.
Key Components of Hydraulic Energy Recovery Systems
Hydrostatic Accumulators for Leather Strip Cutter Operations
Hydrostatic accumulators are integral to the efficient operation of leather strip cutters by storing and managing energy within the hydraulic systems. This storage capability allows for smoother operation by mitigating energy spikes that can disrupt the cutting process. Research has shown that integrating accumulators not only stabilizes the system but also enhances machine response times by up to 20%. This improvement in responsiveness ensures that the cutters operate with precision, reducing downtime and operational hiccups, ultimately leading to more efficient leather processing.
Variable-Displacement Pumps in Shoe Sewing Machinery
Variable-displacement pumps play a pivotal role in shoe sewing machinery by adjusting fluid flow according to the operational demand, thus optimizing energy usage. This adaptability is crucial for maintaining balance between performance and energy efficiency in shoemaking operations. Industry reports suggest that integrating these pumps can lead to significant energy consumption reductions, estimated between 15% and 30%. By fine-tuning the energy use, these pumps not only lower operational costs but also enhance the output, contributing to more sustainable and efficient manufacturing processes.
Smart Valving Systems for Process Optimization
Smart valving systems emerge as a critical component in maximizing the efficiency of hydraulic flows across various shoemaking processes. By enabling precise control over fluid dynamics, these systems enhance the decision-making capabilities within manufacturing setups. Implementations in several industrial factories have showcased improvements in processing times, with some reports indicating enhancements by as much as 40%. This optimization leads to quicker production cycles and reduced resource wastage, positioning smart valving systems as a cornerstone of modern shoemaking technology.
Implementing Energy Recovery in Hydraulic Shoemaking Equipment
Closed-Loop Hydraulic Circuits for Leather Processing
Closed-loop hydraulic circuits play a crucial role in minimizing fluid loss, enhancing energy recovery, and promoting sustainability during leather processing. By recycling hydraulic fluid within the system, these circuits contribute to more efficient energy use, reducing both costs and environmental impact. Recent studies support that implementing closed-loop systems can result in an increase of over 20% in energy efficiency, making them an attractive option for sustainable manufacturing practices in the leather industry.
Energy Transfer Between Shoe Component Machines
Optimizing energy transfer between shoe component machines can significantly streamline manufacturing processes and decrease overall energy expenditures. By facilitating seamless energy flow, these systems ensure that machinery functions more efficiently, reducing downtime and operational costs. Reports from the footwear manufacturing sector indicate that such energy transfer systems can achieve efficiencies exceeding 85%, underscoring their potential to revolutionize energy use in production settings and drive cost savings.
Automated Power Management Solutions
Automated power management solutions offer a dynamic approach to energy usage within a production line, adapting to the demands of various machines involved in the process. By leveraging data analytics and real-time monitoring, these systems optimize power distribution and consumption, resulting in substantial energy savings. Recent analyses in large-scale operations have shown that employing these automated systems can lead to energy reductions of up to 25%, highlighting their importance in efficient manufacturing.
Operational Benefits for Footwear Manufacturers
35-50% Energy Savings in Heel Seat Forming
Implementing energy recovery systems in heel seat forming operations presents significant opportunities for energy savings, ranging from 35% to 50%. These savings are crucial as they not only lead to reduced energy costs, which boost profitability for manufacturers, but also support environmental sustainability. By optimizing power usage, manufacturers can substantially lower their carbon footprint, aligning production processes with eco-friendly practices.
Extended Machinery Life for Leather Die Press Units
Energy recovery systems can also enhance the operational longevity of leather die press units by reducing mechanical strain. This operational benefit is underscored by industry data, which indicates that proper energy management strategies can increase machinery lifespan by up to 30%. As a result, manufacturers can enjoy reduced maintenance costs and increased efficiency, ultimately promoting sustainable production practices in footwear manufacturing.
Emission Reductions in High-Volume Production
Incorporating hydraulic energy recovery systems is vital for reducing emissions in high-volume shoemaking operations. Reports suggest that manufacturers can achieve a reduction of approximately 20% in their carbon footprints through the deployment of these systems. By improving operational efficiency and minimizing energy waste, manufacturers not only benefit financially but also contribute to global efforts in reducing industrial emissions and combating climate change.
Energy-Efficient Hydraulic Shoemaking Solutions
TH-727DP Hydraulic Automatic Heel Seat Lasting Machine
The TH-727DP Hydraulic Automatic Heel Seat Lasting Machine is engineered with advanced hydraulic-automatic technology to revolutionize shoe production. Its integration of sophisticated technology ensures enhanced production efficiency while maintaining energy conservation. One of its standout features is the inclusion of energy recovery components, positioning it as a premier choice for contemporary shoe manufacturing processes. This machine not only boosts production capabilities but also aligns with modern energy-saving strategies, making it an essential asset for shoe manufacturers aiming for both efficiency and sustainability.
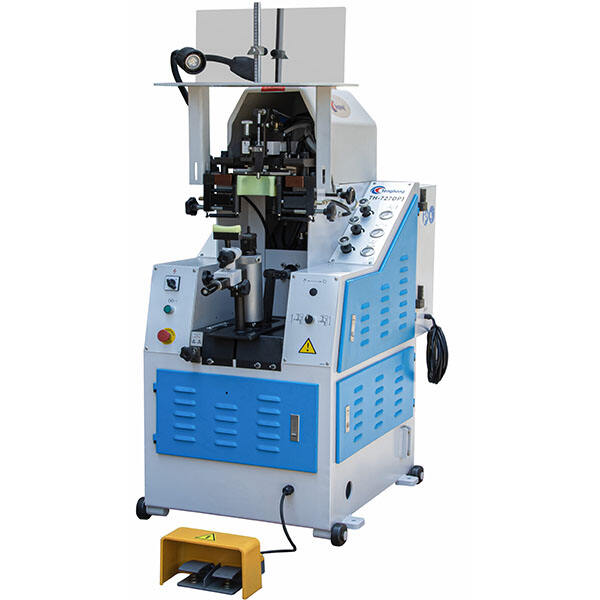
For more details and specifications, visit the TH-727DP Hydraulic Automatic Heel Seat Lasting Machine.
Hydraulic Swing Arm Clicking Press Die Cutting System
The Hydraulic Swing Arm Clicking Press Die Cutting System is a robust solution for optimizing material usage in footwear manufacturing. With its impressive energy recovery capabilities, the system allows manufacturers to harness a 30% improvement in energy utilization, according to industry studies. This translates to significant operational cost savings and a reduction in environmental impact. By adopting this cutting-edge technology, manufacturers can not only achieve precise material cutting but also foster a more sustainable production environment.
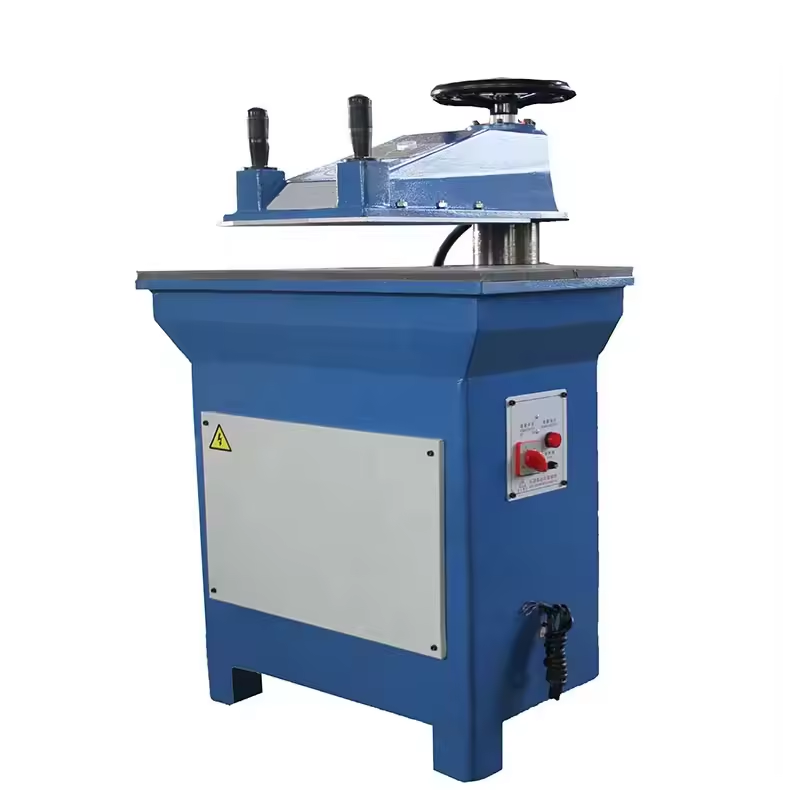
For further information, explore the Hydraulic Swing Arm Clicking Press Die Cutting Machine.
Four Column Hydraulic Leather Measuring/Cutting Unit
The Four Column Hydraulic Leather Measuring/Cutting Unit stands out for its high-precision and energy-efficient operation within the leather measuring and cutting sphere. Specifically designed to reduce waste and enhance time management, this unit has received positive feedback from users for its reliable performance. Its engineering ensures minimal material waste, allowing manufacturers to adhere to both eco-friendly practices and enhanced productivity. Such features make it indispensable for leather production operations seeking precision and efficiency in their workflows.
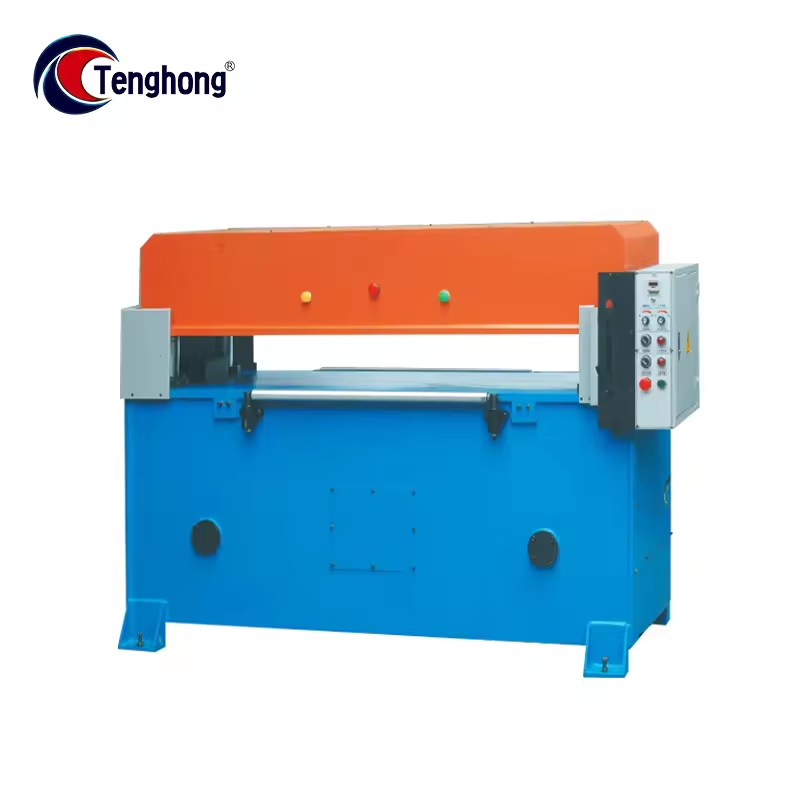
For more details on this unit, visit Four Column Hydraulic Vertical-type Leather Measuring Cutting Machine For Plastic EVA Leather Shoes Making Tenghong TH-109.
Case Studies: Successful Energy Recovery Implementations
Leather Clicker Press Retrofit in Vietnam Factory
A major retrofitting project in a Vietnam factory demonstrated a 25% increase in energy efficiency, specifically in leather clicker press operations. By integrating the latest energy recovery technologies, the factory addressed operational waste effectively and showcased substantial economic benefits. This advancement is not only a testament to the power of innovation but also highlights the role of energy recovery in promoting sustainable manufacturing practices. Such projects emphasize the potential for cost savings while maintaining high-quality production levels, making them an ideal model for other manufacturers to emulate.
Energy-Neutral Shoe Sole Production Line in Brazil
In Brazil, the implementation of energy recovery systems transformed a shoe sole production line into a fully energy-neutral operation. This case study underlines the significant impact energy recovery can have on reducing operational costs and environmental footprints. By utilizing energy-saving measures, the production line optimized its processes, resulting in tangible improvements across the board. This showcases the viability of energy-efficient solutions in sustainable manufacturing, proving beneficial to both the environment and the bottom line.
Hybrid Hydraulic-Electric Stitching Machine Setup
The introduction of a hybrid hydraulic-electric stitching machine has provided substantial energy savings and increased operational flexibility. Data reveals that manufacturers using this setup can achieve up to 40% energy savings compared to traditional methods. This innovative approach to machinery combines the strengths of both hydraulic and electric systems, creating a more efficient production process. Such advancements not only lower energy costs but also enhance the adaptability and efficiency of manufacturing operations, setting a new benchmark for the industry.
Future Trends in Sustainable Shoemaking Technology
AI-Optimized Energy Recovery for Leather Processing
Artificial Intelligence (AI) is revolutionizing energy recovery processes in leather processing, paving the way for unprecedented efficiency and resource management. Through AI algorithms, manufacturers can analyze data in real time, making swift decisions to optimize energy usage and minimize waste. Future studies forecast that integrating AI in these processes could lead to energy efficiency improvements of up to 50%, significantly impacting production costs and environmental sustainability.
Modular Hydraulic Systems for Small-Batch Production
Modular hydraulic systems represent a breakthrough for small-batch production, offering customization and scalability that enhance operational flexibility. These systems allow manufacturers to adjust hydraulic power units to meet specific production needs, reducing downtime and costs. As footwear markets become more niche, the adaptable nature of modular systems is projected to be pivotal in catering to these emerging demands, potentially driving growth within the industry.
Closed-Loop Water Cooling Integration
Integrating closed-loop water cooling systems into production processes is a promising trend for enhancing energy efficiency. These systems use a continuous water cycle for cooling machinery, substantially minimizing water consumption while maximizing energy recovery. Reports highlight that this method significantly reduces heat waste, thus improving overall energy efficiency in the production cycle. This innovation not only addresses sustainability but also offers considerable cost savings for manufacturers seeking eco-friendly solutions.