Customizable Shoe Molds: Adapting Molding Machines for Unique Design Requirements
The Importance of Customizable Shoe Molds in Modern Manufacturing
Meeting Diverse Footwear Design Demands
Customizable shoe molds are pivotal for manufacturers aiming to meet diverse footwear design demands. These molds enable manufacturers to accommodate varying aesthetic and functional needs, which is increasingly critical as consumer preferences shift towards personalized and unique products. Recent surveys highlight that over 60% of consumers actively seek individualized options, indicating a strong market trend. By integrating diverse molds into the production process, manufacturers can enhance their market competitiveness, leading to improved consumer satisfaction and loyalty. This adaptability is essential to capturing consumer interest in a fast-evolving market landscape.
Overcoming Limitations of Standard Molding Equipment
Standard molding equipment often presents significant challenges in accommodating unique designs, resulting in production bottlenecks and elevated costs. Transitioning to customizable molds helps manufacturers overcome these limitations by reducing waste and minimizing labor costs associated with modifying standard molds for specific designs. Statistics reveal that flexible manufacturing systems, which incorporate custom molds, can boost production efficiency by up to 30%. This shift not only streamlines operations but also ensures a seamless adaptation to diverse design requirements, promoting operational agility and cost-effectiveness.
Synergy Between Shoe Molding and Stitching Machines
The synergy between shoe molding and stitching machines greatly enhances the production process, offering significant benefits in efficiency and quality. By integrating customizable molds with advanced stitching technologies, manufacturers can achieve reduced cycle times and improved product quality. Case studies have demonstrated that such synergies can notably shorten lead times, allowing quicker responses to market demands. The seamless collaboration between shoe molding and stitching machines plays a critical role in enhancing production efficiency, ensuring manufacturers stay competitive in a fast-paced industry focused on innovation and rapid delivery.
Technological Innovations in Shoe Molding Machinery
Computerized Control Systems for Precision Molding
Innovative computerized control systems have revolutionized the precision of shoe molding, significantly reducing defects and ensuring product consistency. These cutting-edge systems provide real-time adjustments during the molding process, maintaining high-quality standards while minimizing material waste. Research has shown that automated precision molding can reduce error rates by as much as 40% in footwear production. This reduction not only boosts efficiency but also aligns with sustainability goals, crucial in today's environmentally conscious market.
Multi-Stage Pressure Adjustment Capabilities
Advanced shoe molding machines now often come equipped with multi-stage pressure adjustment capabilities, a feature that enhances the customization of the molding process based on material properties. This technological advancement allows manufacturers to work with a broader variety of materials and improve both the shoe's durability and fit. Industry experts highlight that such capabilities lead to notable improvements in product lifespan and customer satisfaction, ensuring that both performance and comfort are optimized.
Integration with Shoe Polishing Equipment Workflows
Integrating shoe molding machinery with polishing equipment has streamlined production workflows, effectively bridging different manufacturing stages. This synergy in operations not only enhances overall efficiency but also improves quality control, leading to fewer manual interventions. According to empirical studies, fully integrated systems can boost productivity by nearly 25%, demonstrating a significant impact on manufacturing output. By reducing production cycle times and increasing throughput, manufacturers can better meet market demands effectively and efficiently.
TENGHONG Machinery's Custom Molding Solutions
TH-777 9-Pincer Computer Memory Control Automatic Toe Lasting Machine
The TH-777 is equipped with advanced memory control technology, which allows manufacturers to tailor the machine settings to diverse shoe design needs. This ensures that the intricacies of different shoe styles are maintained efficiently. The automation of complex lasting processes significantly boosts production efficiency while offering a reduction in labor expenses. Client feedback consistently reports a remarkable improvement in production speed by up to 20%, achieved without compromising product quality. This automatic toe lasting machine is a testament to TENGHONG Machinery’s commitment to custom molding and innovation.
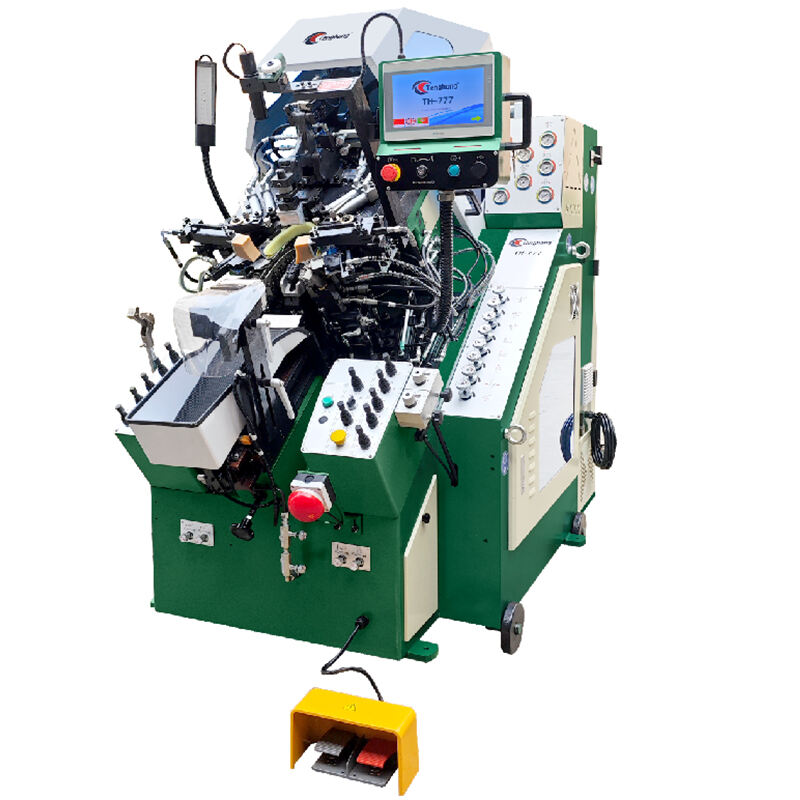
TH-777MA Servo Cementing Toe Lasting Machine with Dual-Stage Features
The TH-777MA machine stands out with its dual-stage features that enable simultaneous operations, effectively speeding up the production cycle. This innovative design offers a cost-efficient solution by delivering precise adhesive applications, which enhance the overall quality of the finished product. Industry analysis highlights that businesses adopting dual-stage technology observe a rapid return on investment, often in less than a year, due to the enhanced efficiency and production rate. TENGHONG Machinery has integrated this design to ensure their clients benefit from state-of-the-art molding solutions that address both quality and operational cost-effectiveness.
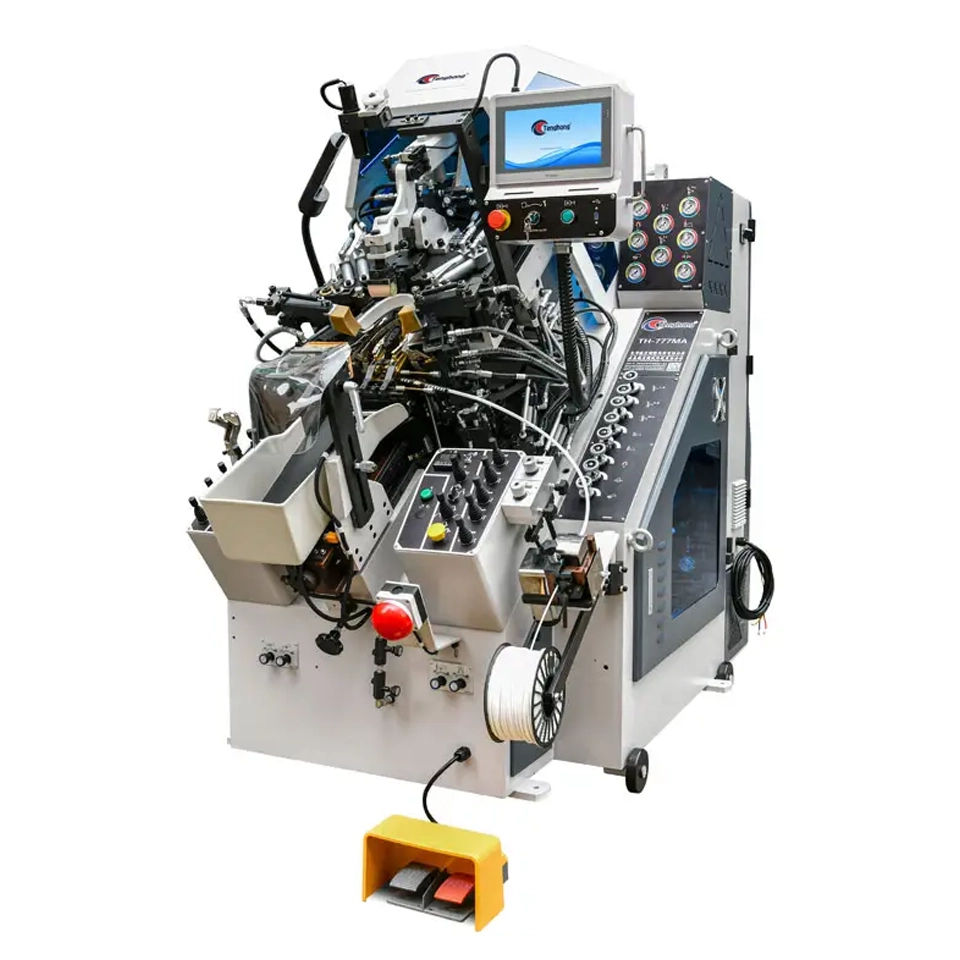
TH-7900 3D Vamp Hot/Cold Molding System
The TH-7900 is a revolutionary system featuring hot and cold molding capabilities that accommodate a wide range of materials, paving the way for versatile shoe designs. This cutting-edge technology is instrumental in achieving superior fit and comfort in footwear, addressing the increasing consumer demand for ergonomic designs. Recent studies have demonstrated that the accuracy of fit afforded by 3D molding technology, such as that in the TH-7900, improves by over 30%, significantly enhancing customer satisfaction and loyalty. With TENGHONG Machinery's commitment to innovation, this equipment embodies progress and precision in shoe production.
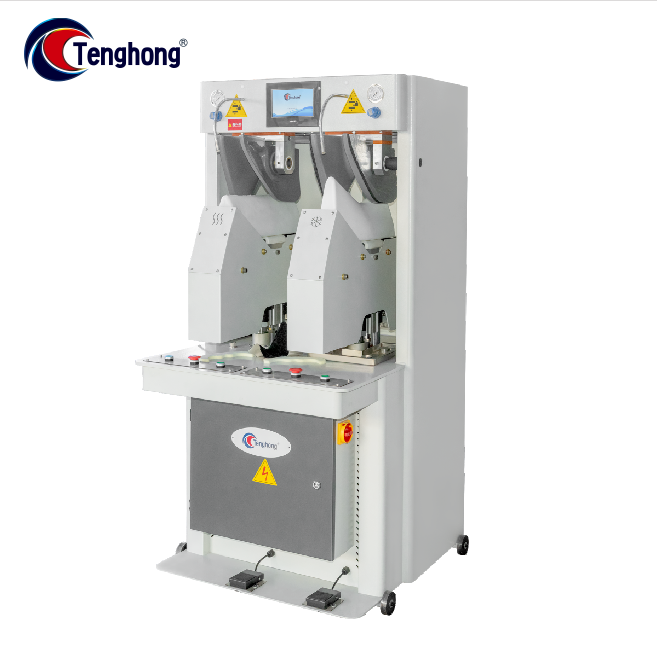
Benefits of Adaptive Shoe Molding Technology
Rapid Prototyping for Unique Shoe Designs
Adaptive shoe molding technology significantly enhances rapid prototyping capabilities, enabling the creation of unique shoe designs efficiently. Designers benefit from this flexibility as it allows them to quickly create and test new concepts, thereby reducing the product development cycle. Data illustrates that brands utilizing rapid prototyping have been able to cut their time to market by approximately 50% compared to traditional methods, showcasing the profound impact on speed and efficiency in product development.
Energy-Efficient Production Processes
Adaptive molding technologies embrace energy-efficient practices within shoe production processes, contributing to sustainable manufacturing. By optimizing power usage during production, manufacturers can substantially reduce their carbon footprint. Reports highlight that innovative energy-efficient techniques can decrease energy consumption by up to 35%, underscoring the environmental benefits of adopting these adaptive technologies in the shoe industry.
Compatibility with Various Material Types
One of the standout benefits of adaptive shoe molding technology is its compatibility with a diverse range of materials, including innovative options like bio-based plastics. This adaptability not only broadens design potential but also aligns with a market trend toward eco-friendly products. Market analysis predicts that demand for such sustainable materials is expected to grow by 15% over the next five years, pointing to a significant shift towards environmentally conscious purchasing decisions.
Future Trends in Custom Shoe Mold Development
AI-Driven Mold Pattern Generation
Artificial intelligence is paving the way for innovative mold pattern generation in the shoe industry, enabling designers to swiftly iterate and optimize footwear designs. This technology leverages machine learning algorithms to assess market trends and consumer preferences, thereby crafting more targeted products. Forecasts expect that the integration of AI could cut down design time by up to 40% over the next decade, making it an essential tool for rapid prototyping and enhancing productivity in shoe molding processes.
Sustainable Material Handling Innovations
The future of shoe mold development is trending towards sustainable materials, propelled by increasing consumer demand and stringent regulatory policies. Advancements in innovative handling techniques are set to further improve the efficiency and sustainability of production processes. Market reports project that sustainable materials could comprise 25% of the shoe production market by 2025, underlining a significant shift towards responsible manufacturing practices.
Modular Systems for Small-Batch Production
Modular systems are revolutionizing shoe molding equipment to support small-batch production, addressing niche markets and custom orders effortlessly. This flexibility allows manufacturers to swiftly transition between various molds, catering to specific customer demands without incurring substantial downtime. Industry analysis indicates that the growing trend of small-batch production could make up about 20% of the overall footwear manufacturing landscape by 2030, showcasing the adaptability and responsiveness these modular systems bring to the production floor.