Optimizing Workflow: The Role of Lasting Machines in Modern Footwear Manufacturing
Core Functions of Lasting Machines in Footwear Production
Precision Shaping for Consistent Product Quality
Lasting machines are fundamental in precisely molding and shaping the shoe upper, ensuring it meets quality and durability standards. By integrating CNC technology, these machines are capable of crafting complex structures consistently, thereby minimizing variations that might compromise product integrity. For instance, statistical data indicates that precision in footwear production can enhance product affinity by over 30%, emphasizing the critical role of lasting machines in maintaining footwear quality. This precision not only elevates product consistency but also boosts customer satisfaction and brand credibility in the highly competitive footwear market.
Integration with Shoe Stitching and Sewing Processes
Lasting machines can be seamlessly integrated with shoe sewing machines like shoe stitch machines, enhancing overall workflow efficiency in footwear production. This integration is key to reducing manual handling, which often leads to inconsistencies, thus streamlining the production process. By automating these elements, manufacturers achieve smoother transitions between stages, leading to a more efficient operation. Expert studies reveal that such integrated systems can result in a 25% reduction in production time, which is significant in meeting the fast-paced demands of the footwear industry. Leveraging automation in this way not only optimizes output but also improves the reliability of the finished product.
Reducing Human Error in Assembly Line Operations
Automated lasting machines play a crucial role in diminishing the reliance on manual labor, thereby decreasing the likelihood of human error in footwear assembly lines. Manual tasks are often error-prone, contributing to over half of the production errors in the footwear industry. By implementing automated solutions, these errors can be significantly reduced. Research suggests this reduction in human errors can enhance product quality and decrease return rates by as much as 18%. This improvement ultimately leads to cost savings for manufacturers and a better end-product for consumers, highlighting the importance of automation in advancing assembly line operations.
Workflow Optimization Strategies Using Modern Machinery
Automated Material Handling Systems
In modern footwear manufacturing, automated material handling systems play a crucial role in optimizing workflow. These systems efficiently manage the transport of materials, reducing the dependency on manual labor, which in turn accelerates production speed and lowers operational costs. Automated systems enhance efficiency significantly, with data suggesting improvements in material handling by up to 40%. By implementing these systems, manufacturers can ensure smoother operations and allocate resources more strategically within the production line.
Real-Time Production Monitoring Capabilities
The integration of real-time production monitoring systems allows footwear manufacturers to instantly assess their production processes, enabling immediate adjustments and corrections. These systems leverage advanced analytics to predict potential failures before they occur, thereby minimizing downtime. According to industry reports, adopting real-time monitoring can boost operational efficiency by nearly 30%. This capability not only improves the decision-making process but also enhances the overall quality and consistency of the production output, paving the way for a more resilient manufacturing environment.
Synchronization with Shoe Polishing & Finishing Stages
Optimizing the workflow in shoe production also requires effective synchronization between the lasting machines and the shoe polishing and finishing stages. This ensures a seamless operation across the production line, adhering to strict production timelines and maintaining product quality. Such synchronization has been evaluated to raise manufacturing quality and reduce lead times by 20%. By harmonizing these stages, manufacturers can achieve a more cohesive and well-orchestrated production process, ultimately resulting in a superior end product ready for market demand.
Advanced Automation Solutions for Footwear Manufacturing
Digital Twin Technology for Process Simulation
Digital twin technology is revolutionizing footwear manufacturing by enabling precise simulation of processes without physical intervention. This advanced technology helps manufacturers test and modify production flows, allowing for efficient optimization and validation of processes. By leveraging digital twins, manufacturers can achieve enhanced design accuracy and significantly reduce development times. Studies indicate that incorporating digital twin technology can decrease design and testing periods by as much as 35%. This reduction streamlines the production pipeline, enabling faster time-to-market and improved responsiveness to market demands.
AI-Driven Quality Control Systems
Artificial Intelligence (AI) has become a cornerstone of quality control in footwear manufacturing, offering continuous monitoring and assessment of product quality. These AI systems are equipped to rapidly analyze defects and suggest corrective actions, greatly enhancing product quality and consistency. Industry reports suggest that AI-driven quality control systems can boost defect detection rates by over 40%, leading to fewer returns and higher customer satisfaction. By automating aspects of quality assurance, footwear manufacturers can maintain high standards while improving efficiency and reducing manual oversight.
Energy-Efficient Operation Modes
In the pursuit of sustainability, modern footwear machinery is increasingly designed with energy-efficient operation modes. These advancements not only curtail operational costs but also lessen the environmental impact of production activities. By integrating energy-saving technologies, manufacturers can achieve notable long-term cost reductions while supporting global sustainability initiatives. Industry analysis highlights that proactive energy efficiency measures can cut energy consumption by an impressive 37%, demonstrating significant potential for cost savings and ecological benefits in footwear manufacturing.
The integration of advanced automation solutions, such as digital twin technology, AI-driven quality control, and energy-efficient machinery, is paving the way for a more efficient and sustainable future in footwear manufacturing. By adopting these modern strategies, manufacturers can enhance productivity, product quality, and environmental stewardship while remaining competitive in the global market.
Innovative Machinery for Enhanced Productivity
TH-308s Vacuum Peeling & Edge Skiving System
The TH-308s Vacuum Peeling & Edge Skiving System is an innovative machine designed to enhance the quality of leather preparation through advanced vacuum peeling technology. This system improves accuracy and efficiency in leather processing, essential for producing high-end footwear. Edge skiving features not only provide a clean finish but also reduce material waste significantly, contributing to both quality and sustainability. Performance metrics from users indicate that employing the TH-308s can boost productivity by approximately 15%, ensuring you meet production goals with fewer resources.
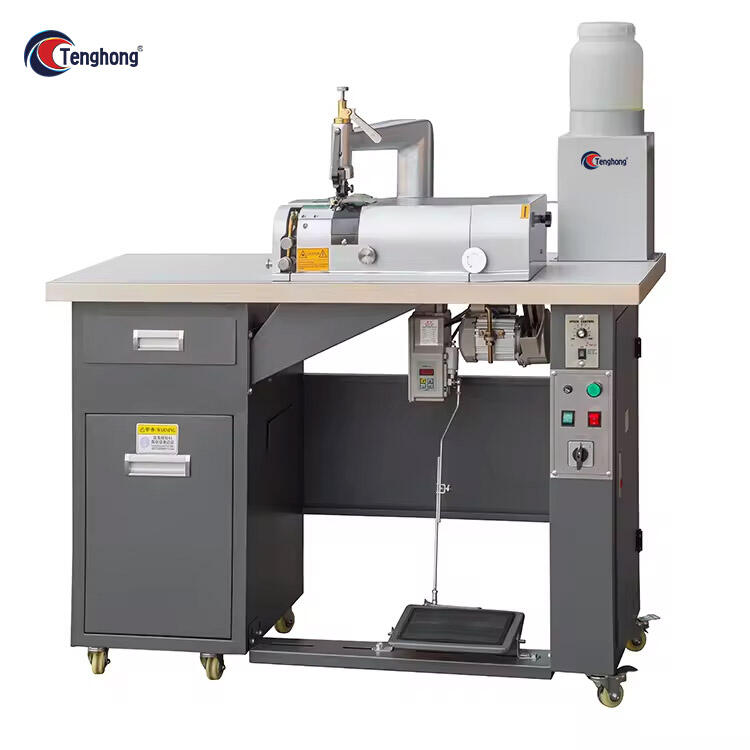
TH-203 Automated Leather Slitting Technology
The TH-203 Automated Leather Slitting Technology offers precise cutting for various leather types, ensuring minimal waste and enhanced material utilization. This model features automated slitting capabilities that reduce the need for manual operation, effectively minimizing errors and significantly speeding up production processes. Analytical reports highlight that the adoption of such automated systems can enhance output consistency by around 20%, making the TH-203 an invaluable asset for manufacturers aiming to optimize leather processing.
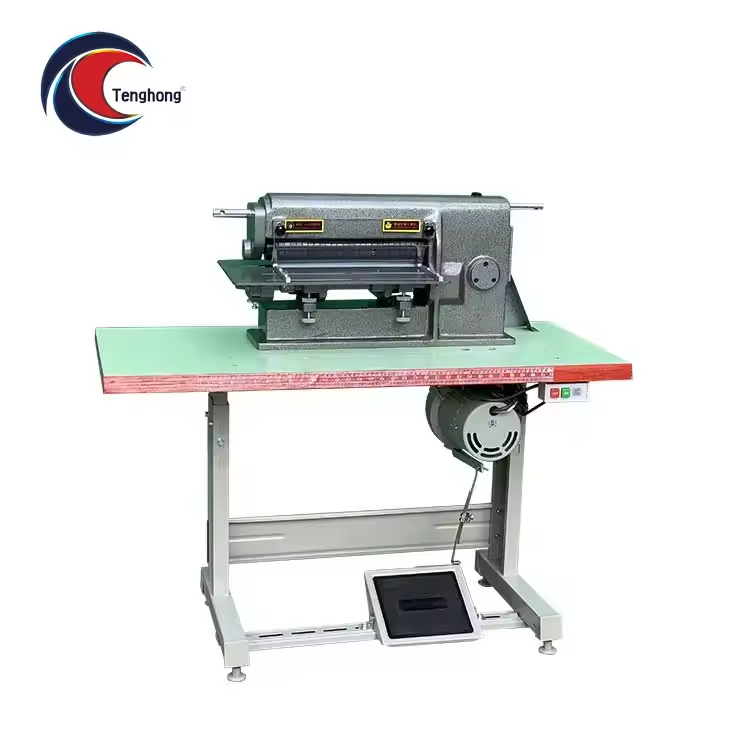
TH-703 Multi-Functional Punching Unit
The TH-703 Multi-Functional Punching Unit showcases exceptional versatility, capable of executing multiple operations including punching, cutting, and shaping. This multifunctionality optimizes workflow by allowing for rapid adjustments in production designs, accommodating diverse manufacturing needs. User reviews have consistently affirmed that the TH-703 greatly enhances operational flexibility, increasing productivity by around 25%. The efficiency offered by this unit makes it an ideal component in comprehensive footwear manufacturing systems.
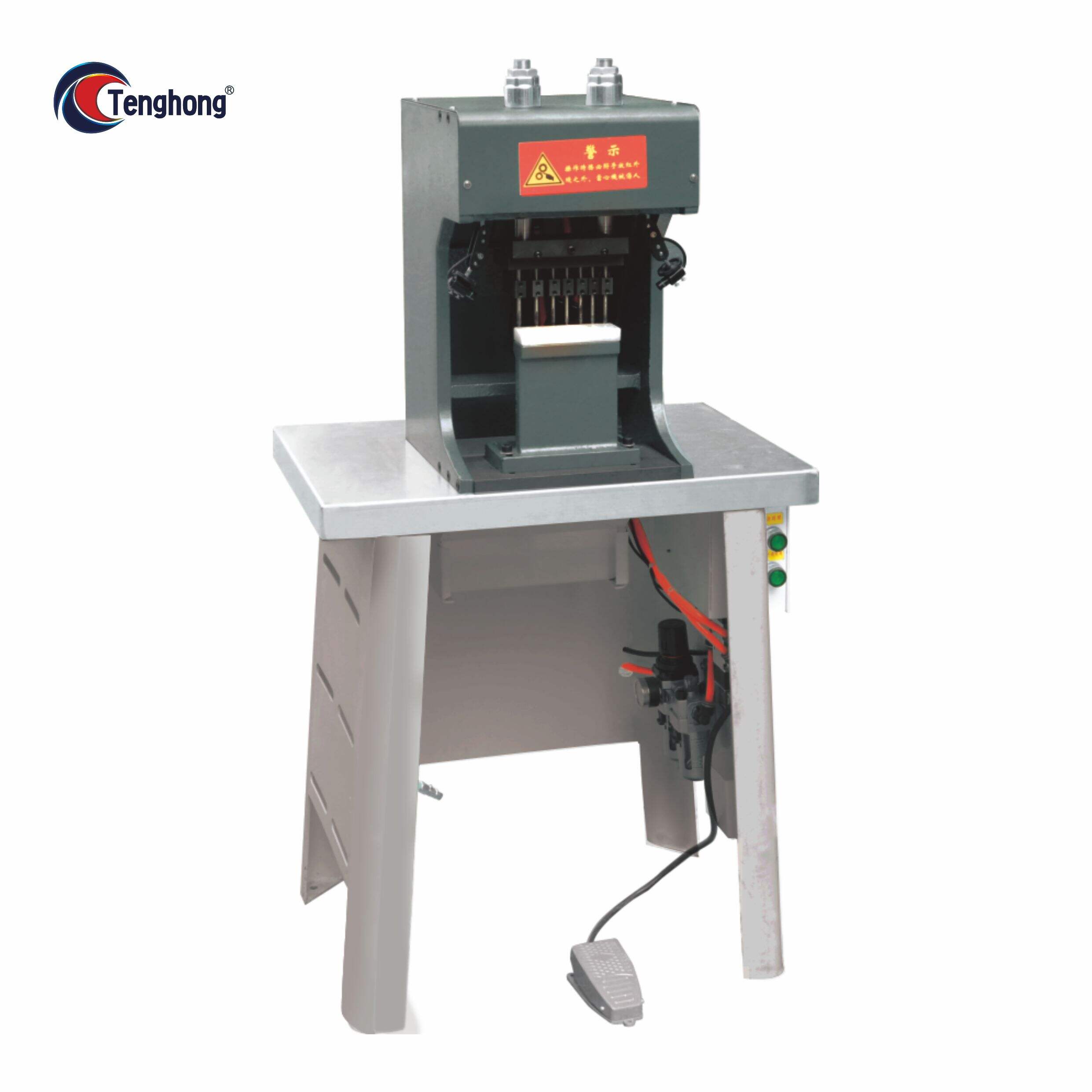
Sustainable Manufacturing & Future Trends
Waste Reduction Through Precision Cutting
Precision cutting technologies are revolutionizing waste reduction in manufacturing. By ensuring cuts are made to exact specifications, these technologies significantly minimize material waste. This not only benefits environmental sustainability but also enhances cost-efficiency. Statistical evidence suggests that precision cutting can reduce scrap rates by up to 30%, providing economic and ecological advantages. Manufacturers increasingly rely on precision techniques to align with sustainable practices and meet industry standards for waste management.
IoT-Enabled Predictive Maintenance Solutions
The integration of IoT in machinery allows for predictive maintenance, transforming traditional maintenance into proactive service strategies. IoT solutions enable real-time monitoring of equipment, signaling when maintenance is necessary beforehand, thus preventing unexpected failures. This proactive approach drastically reduces downtime and elevates operational efficiency. Industry studies highlight that IoT-enabled predictive maintenance can lower maintenance costs by up to 25%, marking it as a significant advancement in machinery upkeep strategies.
Adaptive Systems for Custom Shoe Production
Modern adaptive systems represent a leap forward in custom shoe production, accommodating diverse sizes and styles with ease. These systems cater to the growing consumer demand for personalized footwear, significantly impacting sales. With adaptable technology, manufacturers can swiftly respond to market trends and preferences, enhancing the consumer experience. Market research indicates that companies offering customization options witness a sales increase of 20%, underscoring the importance of personalization in today's market. Adaptive systems are integral to thriving in a competitive footwear industry, leveraging technology to meet consumer demands effectively.