Simplified Sole Attachment: Automating Precision in Shoe Assembly Processes
Key Technologies Revolutionizing Shoe Assembly Automation
PLC Control Systems for Precision Operations
PLC (Programmable Logic Controller) systems significantly enhance precision in shoe assembly by offering accurate control of machinery operations. These systems allow for fine-tuned adjustments to the production process, thereby reducing errors and optimizing efficiency. Studies indicate that the adoption of PLC systems can substantially decrease production downtime, with estimates showing a reduction rate of 10-20%. This improvement in operational efficiency can lead to smoother and faster production cycles. Furthermore, PLC systems integrate seamlessly with other automated technologies, facilitating enhanced data collection and monitoring for continuous improvement in shoe manufacturing processes. Incorporating PLCs in the assembly line can thus revolutionize the way shoes are produced, contributing to higher output quality and consistency.
Hydraulic Press Mechanisms in Sole Attachment
Hydraulic press mechanisms are crucial components in the shoe assembly line, especially during the sole attachment phase. These mechanisms provide uniform pressure essential for maintaining the structural integrity of footwear products. By delivering consistent force across the entire sole, hydraulic systems eliminate the need for manual labor and can complete attachment tasks much quicker than traditional methods. Their efficiency boosts productivity levels significantly, allowing manufacturers to scale up operations effectively. Industry reports suggest that hydraulic systems not only improve productivity but also enhance the quality of finished products by minimizing defects. This attention to quality ensures higher customer satisfaction and reduces returns, making hydraulic presses a valuable asset in shoe manufacturing.
Integration of Vision Systems for Quality Assurance
Vision systems, utilizing advanced imaging technology, are pivotal in the shoe assembly process for ensuring high-quality outputs. These systems inspect the materials and finished products, adhering to strict quality standards and allowing quick detection of defects. This reduces waste and enhances manufacturer reputation, preserving the integrity of the products delivered to consumers. Research findings show that companies implementing vision systems report a 30% reduction in quality-related returns, thereby significantly increasing profitability. Through real-time monitoring and adaptive inspection, vision systems empower manufacturers with insights and data necessary for maintaining superior quality and meeting customer expectations efficiently. By adopting this technology, manufacturers can protect and elevate their brand’s reputation, securing their position in an increasingly competitive industry.
Benefits of Automated Sole Attachment in Footwear Production
Reducing Labor Costs with Shoe Stitch Machines
Automated shoe stitch machines markedly lower labor costs by decreasing reliance on manual labor, enabling manufacturers to allocate human resources to strategic roles. These advanced machines are revolutionizing the footwear industry by allowing businesses to cut labor expenses by up to 30%, bolstering profit margins significantly. This reduction is crucial in an industry constantly striving to stay competitive. By incorporating shoe sewing machines, manufacturers not only save costs but also achieve faster production cycles, enhancing overall efficiency.
Ensuring Consistency in Shoe Making Processes
Automation paves the way for standardized manufacturing processes, crucial for maintaining quality and design integrity. Unlike manual methods which yield around 70% consistency, automated footwear production delivers a remarkable 95% consistency rate. This consistency is vital for brands seeking to uphold their reputation in the market. Automated systems enable manufacturers to efficiently replicate successful designs across various batches, ensuring seamless management of production lines and meeting high standards expected by consumers.
Scalability for High-Volume Manufacturing
Automated sole attachment technology significantly enhances scalability, empowering manufacturers to swiftly increase production volumes in response to market demand without incurring substantial cost hikes. Businesses implementing modular production lines can amplify operations by up to 40%, a feat that is challenging with traditional methods. The inherent flexibility of automation allows manufacturers to adapt swiftly to evolving styles and production requirements, ensuring uninterrupted workflows and positioning them advantageously within the dynamic footwear market.
TengHong Machinery's Advanced Sole Attaching Solutions
TH-710D PLC Control Heavy-Duty Walled Sole Attacher
The TH-710D model from TengHong Machinery exemplifies a robust design, adept at satisfying rigorous production demands while providing consistent performance. Known for its heavy-duty capabilities, this machine is frequently highlighted in user reviews for its efficiency and reliability, making it a top choice for high-output manufacturing settings. It offers highly efficient production, capable of processing up to 120 pairs of shoes per hour, significantly improving productivity rates and establishing its utility as a favorable solution in the competitive shoe manufacturing industry.
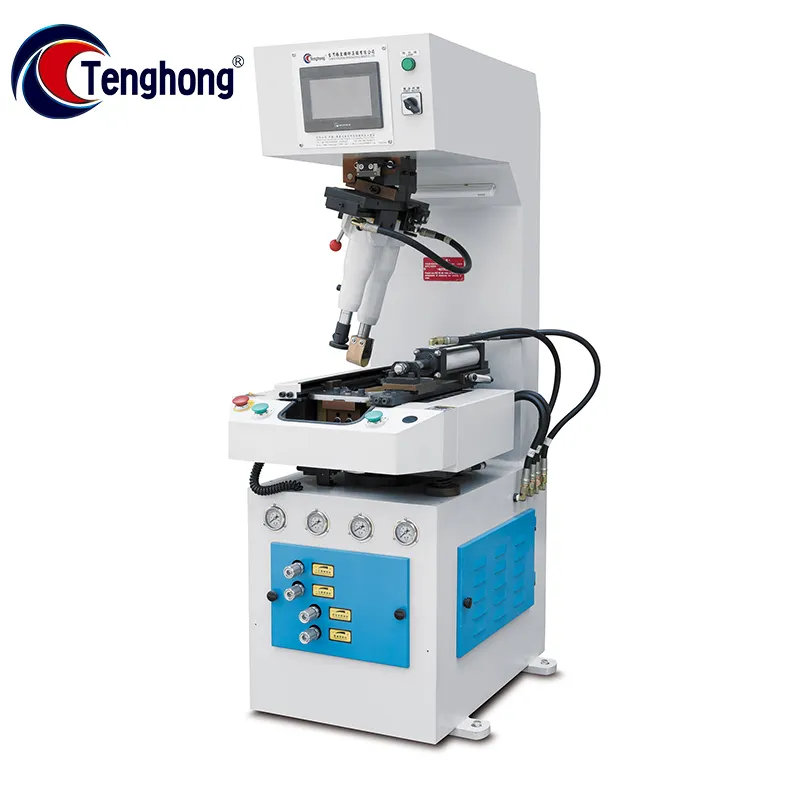
TH-710E Double Station Automation for Diverse Shoe Types
The TH-710E brings remarkable flexibility in production with its double station automation feature, enabling simultaneous processing of various shoe types. This innovation drastically reduces lead times by up to 50%, crucial for manufacturers that need to quickly adapt to the ever-changing fashion trends. The versatility and efficiency in handling multiple styles with minimal downtime during setup changes make it an invaluable asset for shoe manufacturers who prioritize swift response to market demands and product diversity.
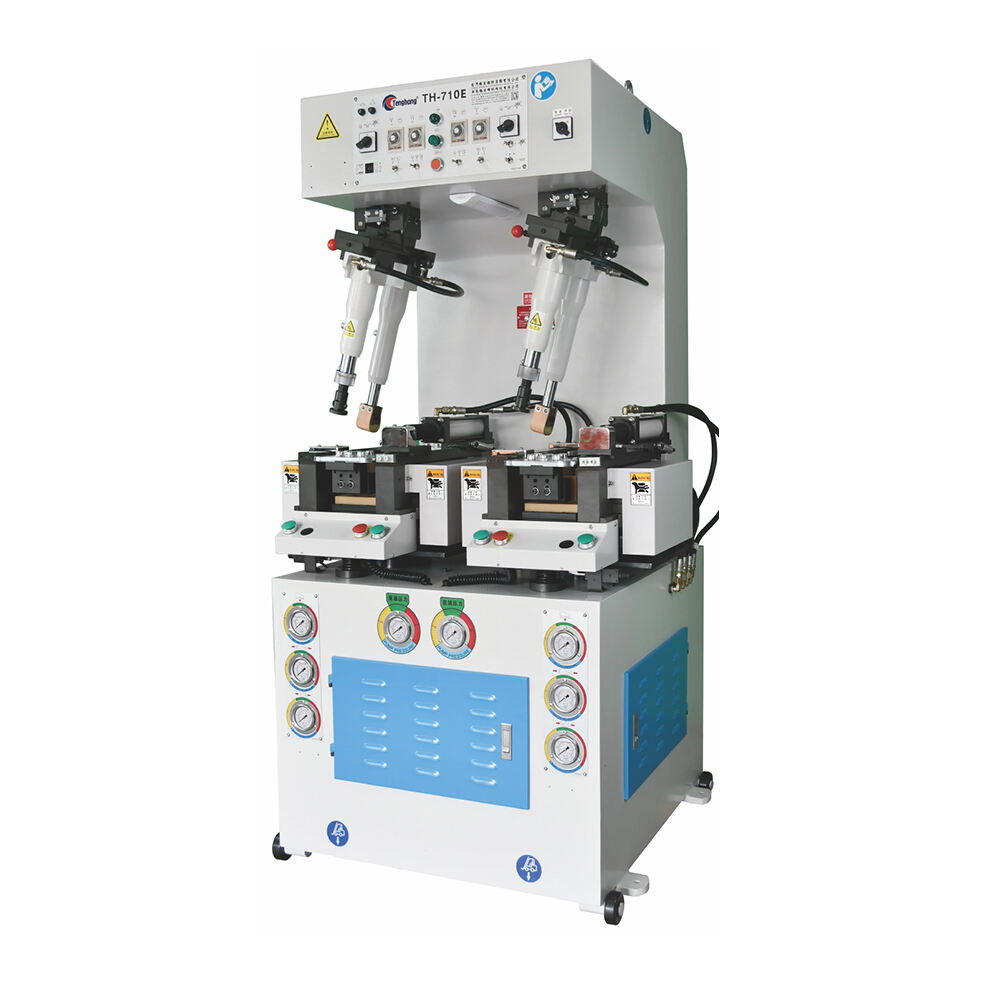
TH-710EU Compact PLC System for Space-Efficient Factories
For operations where space is limited, the TH-710EU offers a compact yet powerful solution. Specifically designed for space-constrained settings, this machine ensures efficient utilization of floor space—improving layout efficiency by up to 20% as clients have reported. Despite its smaller footprint, it delivers performance on par with larger machines, demonstrating how space-efficient designs can match the productivity of more traditional, larger machines without compromising on capability or output.
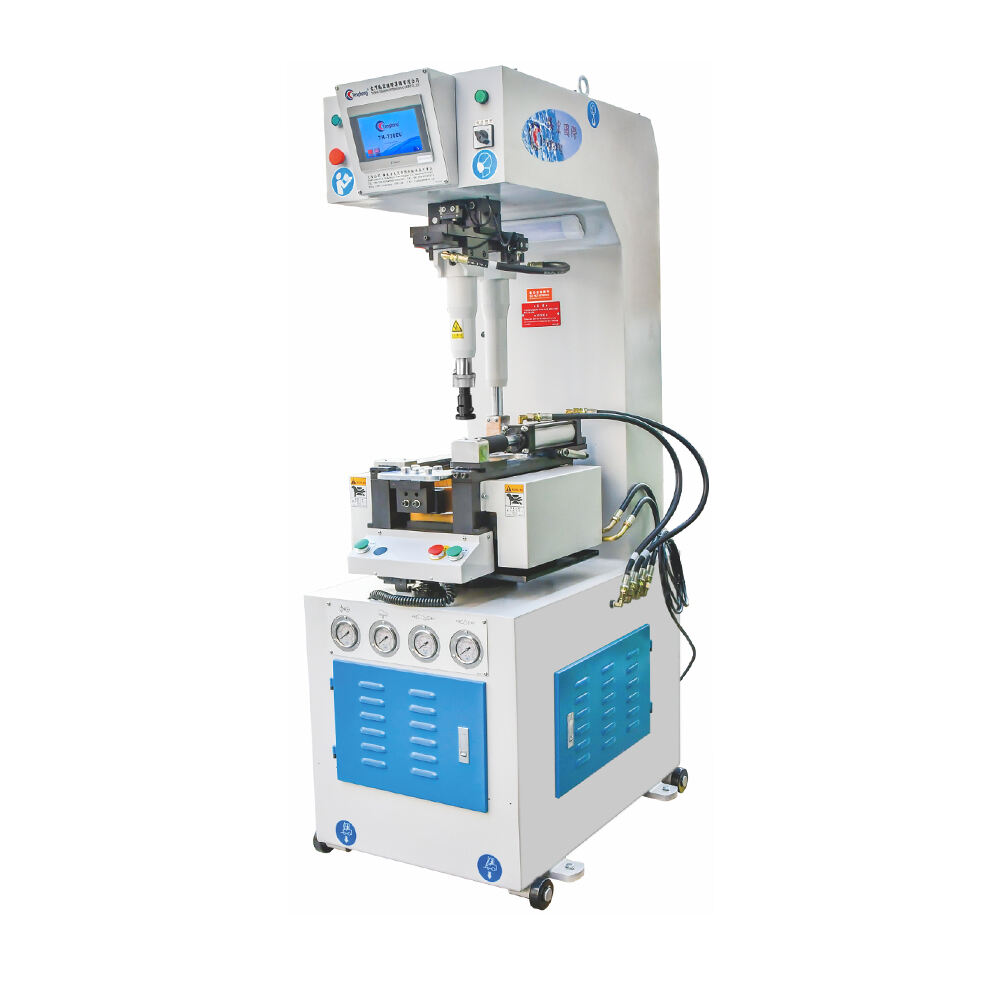
Future Trends in Automated Shoe Manufacturing
AI-Driven Adaptive Shoe Polishing Systems
AI-driven polishing systems are reshaping the shoe manufacturing landscape, offering significant advantages in adaptability and efficiency. These systems can automatically adjust to varying shoe materials and finishes, ensuring consistent, high-quality results across different product lines. Industry experts predict these AI solutions will soon become the standard, given their potential to reduce the manual labor traditionally associated with shoe polishing, thus minimizing inconsistencies. Moreover, adopting AI technology can lead to a substantial 25% reduction in resource consumption by optimizing the polishing process. This not only improves overall production efficiency but also aligns with sustainable manufacturing objectives.
Sustainable Material Handling in Footwear Assembly
The shift towards sustainable practices is becoming increasingly evident in the footwear industry, with automated systems designed for eco-friendly materials leading this transformation. Reports from market analysts suggest that manufacturers embracing sustainability can significantly enhance their competitive edge by appealing to environmentally conscious consumers. Future projections indicate that sustainable material handling systems could potentially reduce waste by up to 40%. This figure highlights the industry's commitment to minimizing its ecological footprint, aligning with a broader global movement towards sustainability. As these technologies continue to evolve, they are expected to play a crucial role in ensuring the industry's longevity and relevance in a rapidly changing market.