Technologie de compensation de force dynamique dans les flux de travail précis des machines à former
Compréhension de la technologie de compensation de force dynamique dans les flux de travail précis
Principes fondamentaux des systèmes de régulation de force
La technologie de compensation de force dynamique est cruciale pour réguler la force dans les processus de précision, en particulier dans le domaine de la fabrication. Elle fonctionne grâce à des systèmes de régulation de force qui utilisent des capteurs avancés et des boucles de rétroaction pour surveiller et ajuster continuellement la force appliquée. Cela garantit que les opérations conservent une haute précision, même lorsque les conditions externes varient. Des exemples de ces systèmes peuvent être observés dans les chaînes d'assemblage automatisées, où l'application précise de la force est essentielle pour maintenir l'intégrité des composants. Ces systèmes utilisent des données en temps réel pour ajuster dynamiquement les forces, minimisant ainsi les erreurs et améliorant l'efficacité. Cette technologie n'est pas seulement théorique ; ses applications pratiques sont déjà visibles dans les secteurs de fabrication qui cherchent à atteindre une précision opérationnelle.
Rôle dans le maintien d'un contact matériel constant
La technologie de compensation de force dynamique joue un rôle important pour garantir un contact matériel constant pendant les processus de fabrication. En ajustant la force appliquée en temps réel, elle minimise le risque de défauts et améliore le contrôle qualité, particulièrement dans des industries comme la fabrication de cuir. Par exemple, les produits en cuir nécessitent un contact constant pour éviter des coupes ou des coutures irrégulières, ce qui pourrait affecter la qualité du produit. Des études indiquent que l'implémentation de cette technologie peut réduire les défauts de production jusqu'à 40 %, améliorant ainsi l'intégrité globale du produit et la satisfaction client. Cela souligne l'importance de la compensation de force dynamique pour maintenir le bon fonctionnement des chaînes de production et garantir des résultats de haute qualité.
Impact sur la précision du décolletage du cuir
Le lien entre la technologie de compensation de force dynamique et la précision du décolletage du cuir est profond. Cette technologie permet un contrôle précis de l'application de la force, ce qui est essentiel pour un décolletage précis. Plusieurs études de cas mettent en avant comment l'intégration de la compensation de force dynamique a considérablement amélioré la précision du décolletage, réduisant ainsi les déchets et le travail de reprise. Les avantages économiques sont importants ; une meilleure précision se traduit par moins de gaspillage de matériaux et une augmentation du débit, ce qui entraîne des économies de coûts pour les fabricants. En substance, l'utilisation de la technologie de compensation de force dynamique n'améliore pas seulement la finesse des opérations de décolletage du cuir, mais offre également des avantages financiers grâce à une efficacité et une qualité de processus accrues.
Composants clés des systèmes de workflow de précision
Configurations de moteurs servo à haute précision
Les moteurs à servocommande à haute précision sont essentiels dans les systèmes de workflow précis. Ces moteurs se distinguent par leur excellente vitesse, couple et réactivité, ce qui les rend indispensables dans les environnements de fabrication performants. Les moteurs à servocommande sont généralement configurés pour offrir un contrôle précis de la position, de la vitesse et de l'accélération, améliorant ainsi l'efficacité des workflows. Par exemple, dans le contexte des machines de production de chaussures, de telles configurations avancées permettent une meilleure précision de couture et de découpe, maximisant le débit tout en minimisant les taux d'erreur. Des études ont montré que l'intégration de moteurs à servocommande à haute précision peut considérablement améliorer les performances de fabrication, en offrant des temps de cycle plus rapides et une meilleure qualité des produits.
Fonctionnement des mécanismes de guidage différentiel expliqué
Les mécanismes d'alimentation différentielle jouent un rôle crucial dans le traitement des matériaux en gérant efficacement le mouvement des matériaux à travers les équipements de traitement. Ces mécanismes permettent des vitesses d'alimentation distinctes pour différentes parties du matériau, garantissant une qualité de traitement constante. En maintenant l'intégrité et la cohérence des matériaux, les mécanismes d'alimentation différentielle réduisent les déformations et les défauts, ce qui est particulièrement important dans des secteurs comme la fabrication textile. En termes d'efficacité, les systèmes utilisant l'alimentation différentielle ont montré une augmentation de jusqu'à 15 % du débit, soulignant leur contribution à l'amélioration des processus de production.
Systèmes de refroidissement par pulvérisation pour l'intégrité des matériaux
Les systèmes de refroidissement par pulvérisation sont cruciaux pour préserver l'intégrité des matériaux dans les applications de production à haute vitesse. Ces systèmes refroidissent rapidement les matériaux en projetant de fines brumes de fluide de refroidissement, réduisant ainsi les déformations causées par la chaleur et préservant la qualité du produit. Les avantages de l'utilisation de systèmes de refroidissement par pulvérisation sont évidents dans des industries comme la mécanique des métaux et la fabrication de plastiques, où maintenir des conditions thermiques précises est essentiel. Par exemple, l'intégration de systèmes de refroidissement par pulvérisation dans la production de pièces automobiles a entraîné une diminution mesurable des taux de défauts, mettant en évidence leur efficacité pour améliorer à la fois les performances et la cohérence.
Applications dans l'automatisation de la fabrication de chaussures
Amélioration des opérations de presse à découper le cuir
La technologie de compensation de force dynamique améliore considérablement l'efficacité des presses à cliquet pour cuir, qui sont au cœur de l'automatisation de la fabrication de chaussures. Cette technologie optimise l'efficacité opérationnelle en ajustant la force appliquée au cuir, permettant des coupes précises à chaque fois. Les rapports indiquent que cet avantage peut réduire les temps de cycle jusqu'à 20 %, permettant aux fabricants de produire davantage avec les mêmes ressources. De plus, une meilleure précision entraîne une réduction du gaspillage de matériaux, un facteur crucial étant donné les coûts liés aux cuirs de haute qualité. Rationaliser les opérations avec cette technologie augmente non seulement la productivité, mais s'aligne également sur les objectifs de durabilité en réduisant l'utilisation globale de matériaux dans les processus de production de chaussures.
Intégration avec les machines à coudre pour chaussures
L'intégration de la technologie de compensation de force dynamique avec les machines à coudre pour chaussures offre des avantages significatifs aux fabricants. Cette combinaison garantit une constance dans la couture et une réduction du taux de défauts, car des ajustements automatiques maintiennent une pression optimale pendant le cousu. Par exemple, les fabricants ont signalé jusqu'à 30 % d'amélioration dans la précision de la couture et une réduction substantielle des retours de produits dus à des défauts. Les témoignages des principaux fabricants de chaussures soulignent les avantages, en citant une amélioration de la qualité du produit et une augmentation de la satisfaction client. En associant ces machines à une technologie de pointe, les fabricants peuvent résoudre les défis de production courants, ce qui conduit à une durabilité et une esthétique améliorées des produits.
Optimisation des rendements des machines de production de chaussures
La technologie de compensation de force dynamique joue un rôle essentiel dans l'optimisation des rendements des machines de production de chaussures. En surveillant et en ajustant continuellement les paramètres de production, cette technologie garantit une efficacité et une productivité maximales. Une surveillance améliorée de la production aide à identifier les problèmes potentiels tôt, permettant des ajustements opportuns qui renforcent l'efficacité opérationnelle. Par exemple, les entreprises utilisant de tels systèmes ont signalé une augmentation notable de l'efficacité énergétique et une amélioration de 25 % de l'utilisation des matériaux, mettant en lumière les avantages financiers et environnementaux. Ces progrès marquent un bond vers une production de chaussures plus durable et économique, répondant aux exigences de l'industrie en matière d'augmentation de la production et de l'efficacité.
Solutions Avancées de TengHong Machinery
Caractéristiques de la Machine de Découpe par Vide TH-308s
Le Machine de Découpe par Vide TH-308s est un outil révolutionnaire dans la fabrication moderne de chaussures, où ses fonctionnalités avancées répondent aux exigences en évolution constante de l'industrie. Cette machine met en avant des technologies brevetées et un design précis qui optimisent les opérations tout en offrant une grande précision et une durabilité accrue. Les caractéristiques clés incluent un système de refroidissement unique avec des tailles de brouillard ajustables, adapté à différents matériaux lors du traitement. Cette fonction seule améliore non seulement l'efficacité opérationnelle, mais réduit également l'usure des composants de la machine. De plus, le TH-308s prend en charge une large gamme de matériaux grâce à son alimentation différentielle adaptative, le rendant approprié pour les bords de matériaux épais comme fins. Les spécifications techniques de la machine, telles qu'une largeur de travail allant jusqu'à 50 mm et une plage d'épaisseur de traitement de 0,5 à 5 mm, soulignent encore davantage ses capacités d'application étendues, confirmées par des retours d'utilisateurs positifs.
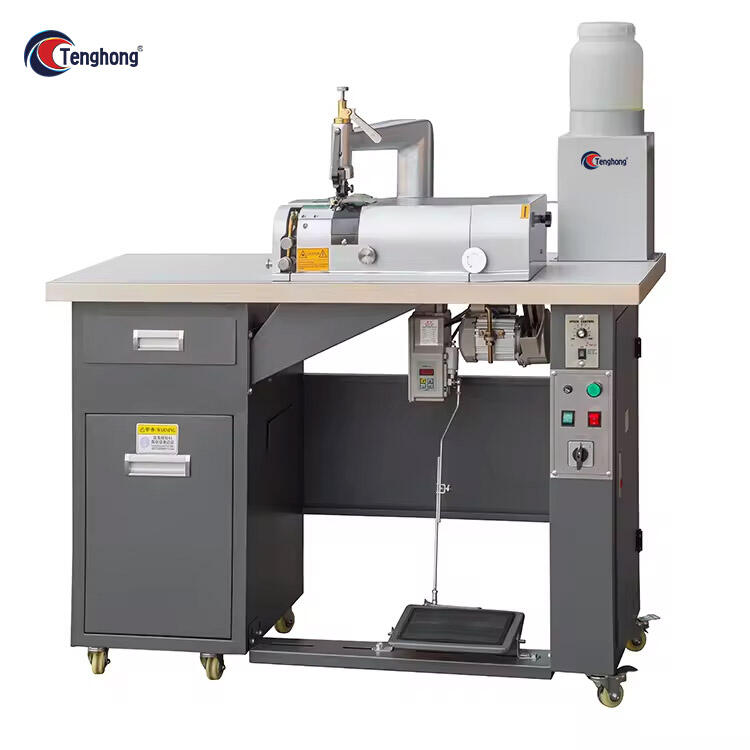
Capacités de la machine à ébarber à double entraînement direct
Le Machine à ébarber à double entraînement direct représente un progrès dans la fabrication de chaussures à haute précision, offrant des avantages significatifs tels que des pertes mécaniques réduites et des performances accrues. Cette machine intègre une technologie de moteur direct qui minimise la dissipation d'énergie et améliore la fiabilité opérationnelle, essentielle pour produire des résultats constants et de haute qualité. Son design axé sur la précision est particulièrement bénéfique pour les opérations de découpe, garantissant des surfaces de coupe lisses et uniformes adaptables aux différentes épaisseurs de matériaux. De nombreux utilisateurs ont signalé des améliorations, avec une meilleure fluidité de coupe et une efficacité accrue dans la manipulation des matériaux. De plus, les études de cas montrent comment les entreprises ont exploité cette technologie pour optimiser leurs processus de production, témoignant de la capacité de la machine à gérer aussi bien les matériaux rigides que flexibles avec facilité et précision.
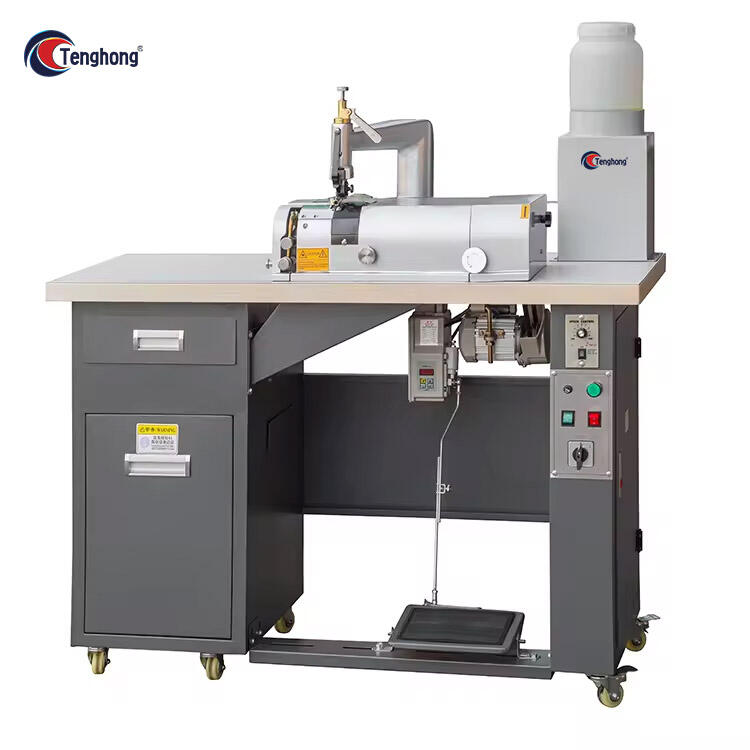
Optimisation des paramètres de traitement des matériaux
Ajustement pour des variations d'épaisseur de 0,5 à 5 mm
L'ajustement des machines pour accommoder les variations d'épaisseur du matériau est crucial pour optimiser l'efficacité et la qualité de production. Comme les matériaux varient entre 0,5 et 5 mm d'épaisseur, les machines doivent être correctement calibrées pour maintenir une cohérence des produits et réduire le gaspillage. La mise en œuvre de bonnes pratiques, telles que la vérification périodique des réglages des machines et l'utilisation de capteurs avancés pour détecter les écarts, garantit une performance optimale des machines même avec des variations d'épaisseur. Les recommandations d'experts issus des leaders de l'industrie soulignent l'importance des vérifications de calibration régulières pour s'adapter aux différentes épaisseurs de matériaux et assurer des opérations de production fluides.
applications de largeur d'affinage plane de 50 mm
L'application d'une largeur de rabotage plane de 50 mm trouve sa place dans divers environnements de production, en particulier dans le secteur de la fabrication de chaussures. Cette largeur spécifique permet un rabotage précis du matériau, ce qui est crucial pour créer des couches uniformes pour divers composants. Cependant, des défis techniques tels que le maintien de l'uniformité sur de grands volumes peuvent se poser. Des solutions comme l'utilisation de réglages de pression constants et une maintenance régulière des équipements aident à atténuer ces problèmes. Des exemples tirés de la production de chaussures mettent en évidence comment ces processus contribuent à fabriquer des chaussures de haute qualité, démontrant la nécessité et l'efficacité des applications de rabotage précis dans la production industrielle.
Régulation de la vitesse pour différents matériaux
Le réglage de la vitesse joue un rôle pivot dans le traitement efficace de différents matériaux, influençant la qualité et l'efficacité de la production. Différents matériaux nécessitent des réglages de vitesse spécifiques pour obtenir des résultats optimaux sans compromettre leur intégrité. Des lignes directrices, telles que l'ajustement de la vitesse en fonction de la densité et de la résistance du matériau, fournissent un cadre pour un réglage de vitesse efficace. Les insights d'experts, mettant en avant l'importance de la collecte de données empiriques pendant la phase de production, offrent des techniques précieuses pour affiner ces ajustements. Ces pratiques assurent non seulement les résultats souhaités, mais augmentent également la productivité, se révélant essentielles pour maintenir de hauts standards dans la fabrication.