Dynamische Kraftkompensationstechnologie in präzisen Strickmaschinen-Arbeitsabläufen
Verstehen der Dynamischen Kraftkompensationstechnologie in Präzisionsabläufen
Kernprinzipien von Kraftregelsystemen
Die Technologie der dynamischen Kraftkompensation ist entscheidend für die Regelung von Kräften in präzisen Arbeitsabläufen, insbesondere in der Fertigung. Sie arbeitet mit Kraftregelsystemen, die fortgeschrittene Sensoren und Feedback-Schleifen nutzen, um angewandte Kräfte kontinuierlich zu überwachen und anzupassen. Dadurch wird sichergestellt, dass Vorgänge eine hohe Genauigkeit aufrechterhalten, selbst wenn äußere Bedingungen schwanken. Beispiele dieser Systeme können in automatisierten Montagelinien gesehen werden, wo eine präzise Kraftanwendung entscheidend für die Integrität der Komponenten ist. Diese Systeme nutzen Echtzeitdaten, um Kräfte dynamisch anzupassen, wodurch Fehler minimiert und die Effizienz gesteigert wird. Diese Technologie ist nicht nur theoretisch; ihre praktischen Anwendungen sind bereits in Fertigungssektoren sichtbar, die nach operationeller Präzision streben.
Rolle bei der Aufrechterhaltung eines konsistenten Materialkontakts
Die Technologie der dynamischen Kraftkompensation spielt eine bedeutende Rolle bei der Sicherstellung einer konsistenten Materialkontakte während von Fertigungsprozessen. Durch die Echtzeit-Anpassung der angewendeten Kraft minimiert sie das Risiko von Fehlern und verbessert die Qualitätskontrolle, insbesondere in Branchen wie der Lederherstellung. Zum Beispiel benötigen Lederprodukte einen konstanten Kontakt, um ungleichmäßige Schnitte oder Nahtungen zu vermeiden, was die Produktqualität beeinträchtigen könnte. Studien zeigen, dass die Implementierung dieser Technologie die Anzahl der Produktionsfehler um bis zu 40 % reduzieren kann, was die Gesamintegrität des Produkts und die Kundenzufriedenheit erhöht. Dies unterstreicht die Bedeutung der dynamischen Kraftkompensation bei der Aufrechterhaltung eines reibungslosen Betriebs von Fertigungslinien und der Sicherstellung hoher Qualitätsergebnisse.
Auswirkungen auf die Schichtengenauigkeit von Leder
Die Beziehung zwischen Dynamik-Kompensationstechnologie und Lederschälergenauigkeit ist tiefgreifend. Diese Technologie ermöglicht eine präzise Kontrolle der Kraftanwendung, was für eine genaue Schälung unerlässlich ist. Mehrere Fallstudien betonen, wie die Integration von Dynamik-Kompensation die Schälgenauigkeit erheblich verbessert hat, wodurch Verschwendung und Nacharbeit reduziert werden. Die wirtschaftlichen Vorteile sind erheblich; eine verbesserte Genauigkeit führt zu weniger Materialverschwendung und einem erhöhten Durchsatz, was zu Kosteneinsparungen für Hersteller führt. Im Wesentlichen bietet die Verwendung von Dynamik-Kompensationstechnologie nicht nur einen Fortschritt in der Präzision der Lederschäloperationen, sondern bietet auch finanzielle Vorteile durch eine verbesserte Prozess-effizienz und Qualität.
Schlüsselkomponenten von Präzisionsworkflow-Systemen
Hochpräzise Servomotor-Konfigurationen
Hochpräzise Servomotoren sind integraler Bestandteil von Präzisionsworkflow-Systemen. Diese Motoren zeichnen sich durch ihre hervorragende Geschwindigkeit, Drehmoment und Reaktionsfähigkeit aus, was sie in leistungsstarken Fertigungsumgebungen unverzichtbar macht. Servomotoren werden normalerweise so konfiguriert, dass sie eine präzise Steuerung der Position, Geschwindigkeit und Beschleunigung bieten, was die Effizienz von Workflows erhöht. Zum Beispiel führen solche fortschrittlichen Konfigurationen bei Schuhproduktionsmaschinen zu einer besseren Näh- und Schneidpräzision, maximieren den Durchsatz und minimieren Fehlerquoten. Studien haben gezeigt, dass die Integration hochpräziser Servomotoren die Fertigungsleistung erheblich verbessern kann, indem kürzere Zyklenzeiten und eine bessere Produktqualität erreicht werden.
Differentialfütterungsmechanismen erklärt
Differentialfütterungsmechanismen spielen eine entscheidende Rolle bei der Materialverarbeitung, indem sie die Bewegung von Materialien durch Verarbeitungsanlagen effektiv steuern. Diese Mechanismen ermöglichen unterschiedliche Fütterungsgeschwindigkeiten für verschiedene Teile des Materials, was eine konsistente Verarbeitungsqualität gewährleistet. Durch die Aufrechterhaltung der Integrität und Konsistenz der Materialien reduzieren Differentialfütterungsmechanismen Verformungen und Fehler, was insbesondere in Branchen wie der Textilherstellung von großer Bedeutung ist. Hinsichtlich der Effizienz haben Systeme mit Differentialfütterung einen Durchsatzanstieg von bis zu 15 % erzielt, was ihre Beiträge zu verbesserten Produktionsprozessen unterstreicht.
Spray Kühlungssysteme zur Sicherung der Materialintegrität
Spray-Kühlsysteme sind entscheidend für die Erhaltung der Materialintegrität in Hochgeschwindigkeitsproduktionsanwendungen. Diese Systeme kühlen Materialien durch das Sprühen feiner Kühlnebel schnell ab, wodurch wärmebedingte Verformungen reduziert und die Produktqualität erhalten wird. Die Vorteile der Verwendung von Spray-Kühlsystemen zeigen sich in Branchen wie der Metallbearbeitung und der Kunststoffherstellung, wo die Einhaltung präziser thermischer Bedingungen essenziell ist. Zum Beispiel hat die Integration von Spray-Kühlsystemen in der Produktion von Automobilteilen zu einer messbaren Verringerung der Defektrate geführt, was ihre Wirksamkeit bei der Verbesserung von Leistung und Konsistenz unter Beweis stellt.
Anwendungen in der Schuhfertigung-Automatisierung
Verbesserung der Lederschneidpresse-Operationen
Die Technologie der dynamischen Kraftkompensation verbessert erheblich die Effizienz von Lederschlagpressen, die zentral für die Automatisierung des Schuhherstells sind. Diese Technologie erhöht die Betriebswirksamkeit, indem sie die auf Leder angewendete Kraft anpasst und so präzise Schnitte bei jedem Durchgang ermöglicht. Berichte deuten darauf hin, dass dieser Fortschritt die Taktzeiten um bis zu 20 % verkürzen kann, was den Herstellern ermöglicht, mehr mit denselben Ressourcen zu produzieren. Darüber hinaus führt eine bessere Präzision zu einem reduzierten Materialverbrauch, ein entscheidender Faktor bei den Kosten hochwertiger Lederarten. Die Streamlining-Operationen mit dieser Technologie steigert nicht nur die Produktivität, sondern deckt sich auch mit Nachhaltigkeitszielen, indem insgesamt weniger Material in den Produktionsprozessen für Schuhe verbraucht wird.
Integration in Schuhnähmaschinen
Die Integration von Dynamik-Kraftkompensationstechnologie mit Schuhnähmaschinen bietet den Herstellern erhebliche Vorteile. Diese Kombination gewährleistet eine konsistente Nähqualität und reduziert die Defektrate, da automatische Anpassungen während des Nähausgangs den optimalen Druck aufrechterhalten. Zum Beispiel haben Hersteller eine bis zu 30 % bessere Nähgenauigkeit gemeldet sowie eine erhebliche Reduktion der Rückgaben aufgrund von Fehlern verzeichnet. Zeugnisse führender Schuhhersteller unterstreichen diese Vorteile, indem sie eine verbesserte Produktqualität und erhöhte Kundenzufriedenheit nennen. Durch das Paaren dieser Maschinen mit neuester Technologie können Hersteller übliche Produktionsprobleme lösen, was sich in einer gesteigerten Produkthaftbarkeit und ästhetischen Erscheinung widerspiegelt.
Optimierung der Ausgänge von Schuhproduktionsmaschinen
Die Technologie der dynamischen Kraftkompensation spielt eine entscheidende Rolle bei der Optimierung von Ausgaben in Schuhproduktionsmaschinen. Durch ständiges Überwachen und Anpassen von Produktionsparametern stellt diese Technologie maximale Effizienz und Produktivität sicher. Verbessertes Produktionsmonitoring hilft, potenzielle Probleme frühzeitig zu erkennen, was rechtzeitige Anpassungen ermöglicht, die die operative Effizienz steigern. Zum Beispiel haben Unternehmen, die solche Systeme verwenden, einen bemerkenswerten Anstieg der Treibstoffeffizienz und eine 25-prozentige Steigerung der Materialausnutzung gemeldet, was die finanziellen und umweltschützenden Vorteile unterstreicht. Diese Fortschritte bedeuten einen Sprung hin zu nachhaltigerer und kostengünstigerer Schuhproduktion, wobei den Branchenforderungen nach höherer Ausgabe und Effizienz gerecht wird.
TengHong Machinery's Fortgeschrittene Lösungen
Funktionen der TH-308s-Vakuumentfernungs-Maschine
Die TH-308s Vakuumentfernungs-Maschine ist ein bahnbrechendes Werkzeug in der modernen Schuhherstellung, wobei seine fortschrittlichen Funktionen den sich wandelnden Anforderungen der Branche gerecht werden. Diese Maschine hebt patentierte Technologien und eine präzise Gestaltung hervor, die Prozesse vereinfachen, während sie hohe Genauigkeit und Dauerhaftigkeit bieten. Zu den wichtigsten Funktionen gehört ein einzigartiges Kühlungssystem mit verstellbaren Tröpfchengrößen, das auf verschiedene Materialien während der Verarbeitung zugeschnitten ist. Allein diese Funktion verbessert nicht nur die Betriebs-effizienz, sondern verringert auch Verschleiß an den Maschinenteilen. Darüber hinaus unterstützt die TH-308s eine Vielzahl von Materialien dank ihrer anpassungsfähigen Differentialfütterung, was sie für sowohl dicke als auch dünne Materialkanten geeignet macht. Die technischen Spezifikationen der Maschine, wie eine Arbeitsbreite von bis zu 50 mm und eine Verarbeitungsdicke von 0,5-5 mm, unterstreichen weiter ihre vielseitigen Einsatzmöglichkeiten, bestätigt durch positive Benutzererfahrungen.
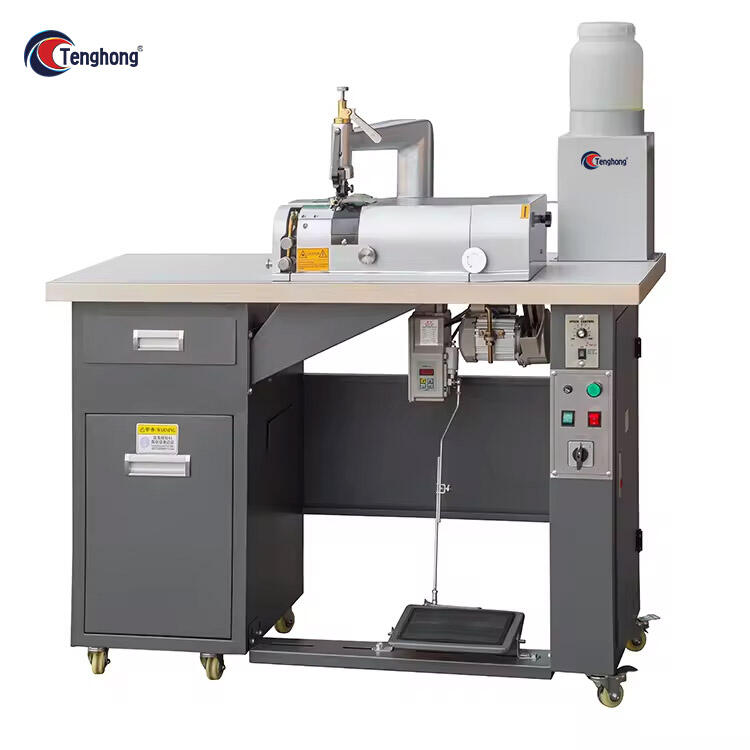
Fähigkeiten der Doppeldirektantriebs-Skiving-Maschine
Die Doppeldirektantriebs-Skiving-Maschine stellt einen Sprung in der Hochpräzisions-Fertigung von Schuhen dar und bietet erhebliche Vorteile wie weniger mechanische Verluste und verbesserte Leistung. Diese Maschine integriert Direktantriebstechnologie, die Energieverluste minimiert und die Betriebszuverlässigkeit erhöht – entscheidend für konsistente, hochwertige Ausgaben. Ihr präzisionsorientiertes Design ist insbesondere bei Beschneidungsoperationen von Vorteil, da es glatte und gleichmäßige Schnittflächen sicherstellt, die sich an unterschiedliche Materialstärken anpassen. Viele Nutzer berichten über verbesserte Ergebnisse mit erhöhter Schnittglätte und Effizienz im Umgang mit Materialien. Darüber hinaus zeigen Fallstudien, wie Unternehmen diese Technologie genutzt haben, um ihre Produktionsprozesse zu optimieren und dass die Maschine sowohl starre als auch flexible Materialien mit Leichtigkeit und Präzision verarbeiten kann.
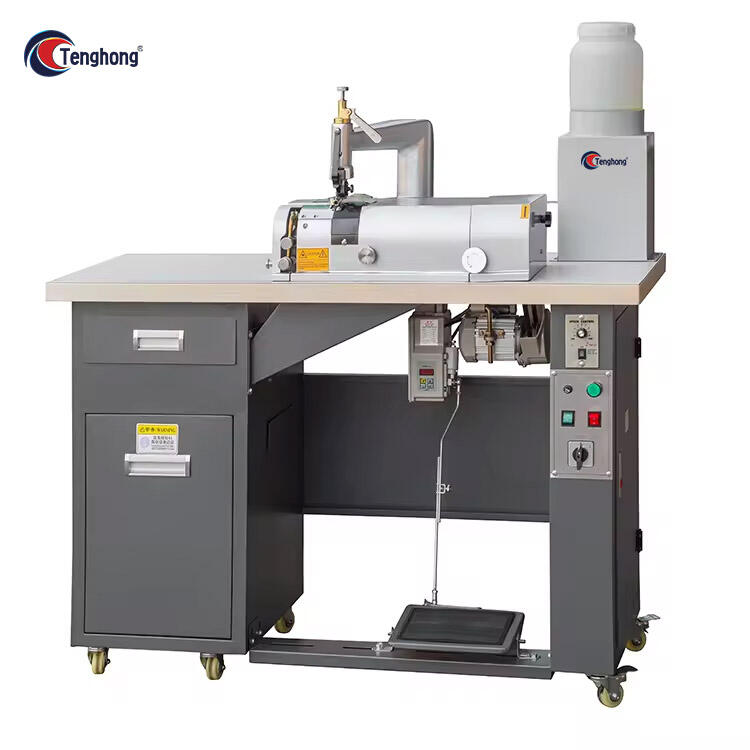
Optimierung der Materialbearbeitungsparameter
Anpassung für Dickenunterschiede von 0,5-5mm
Die Anpassung von Maschinen an Dickenunterschiede des Materials ist entscheidend für die Optimierung der Produktionswirksamkeit und Qualität. Während Materialien zwischen 0,5-5mm dick variieren, müssen Maschinen entsprechend kalibriert werden, um Produktkonsistenz zu gewährleisten und Verschwendung zu reduzieren. Die Implementierung bewährter Verfahren, wie regelmäßiges Überprüfen der Maschineneinstellungen und das Nutzen fortschrittlicher Sensoren zur Erkennung von Abweichungen, stellt sicher, dass die Maschine selbst bei Dickenunterschieden optimal leistet. Expertenempfehlungen von Branchenführern sehen regelmäßige Kalibrierkontrollen als essentiell an, um sich an unterschiedliche Materialdicken anzupassen und reibungslose Produktionsprozesse sicherzustellen.
anwendungen für 50mm ebene Dünnungsbreite
Die Anwendung einer 50-mm-Ebene für das Dünnenschälen findet ihren Platz in unterschiedlichen Produktionsumgebungen, insbesondere im Schuhproduktionssektor. Diese spezifische Breite ermöglicht eine präzise Materialverdünnung, was bei der Erstellung gleichmäßiger Schichten für verschiedene Komponenten entscheidend ist. Allerdings können technische Herausforderungen wie die Wahrung der Gleichmäßigkeit bei großen Chargen auftreten. Lösungen wie die Verwendung konsistenter Druckeinstellungen und regelmäßige Wartung der Ausrüstung helfen, diese Probleme zu mindern. Beispiele aus der Schuhproduktion verdeutlichen, wie diese Prozesse zur Herstellung hochwertiger Schuhe beitragen und die Notwendigkeit und Effizienz präziser Dünnenschälungsanwendungen in der industriellen Produktion demonstrieren.
Geschwindigkeitsregelung für verschiedene Materialien
Die Geschwindigkeitsregelung spielt eine entscheidende Rolle bei der effektiven Verarbeitung unterschiedlicher Materialien, wodurch sich die Produktionsqualität und -effizienz beeinflussen lassen. Verschiedene Materialien erfordern spezifische Geschwindigkeitseinstellungen, um optimale Ergebnisse zu erzielen, ohne deren Integrität zu gefährden. Leitlinien, wie die Anpassung der Geschwindigkeit anhand der Materialdichte und -widerstandsfähigkeit, bieten einen Rahmen für eine wirksame Geschwindigkeitsregelung. Expertenmeinungen, die auf die Bedeutung der Datensammlung während der Produktionsphase hinweisen, bieten wertvolle Techniken zur Feinabstimmung dieser Einstellungen. Diese Praktiken gewährleisten nicht nur die gewünschten Ergebnisse, sondern steigern auch die Produktivität und sind somit essenziell für den Erhalt hoher Standards in der Fertigung.