بروتوكولات الصيانة التنبؤية لتعزيز كفاءة خطوط الإنتاج المستمرة
أسس الصيانة التنبؤية للإنتاج المستمر
المكونات الأساسية للبروتوكولات الفعالة
إنشاء أساس صلب للصيانة التنبؤية يتطلب تحديد المكونات الأساسية اللازمة لتنفيذ ناجح. وتشمل هذه عادةً مراقبة حالة المعدات، تحليل البيانات، واستراتيجية صيانة مصممة لتتوافق مع أهداف الإنتاج. تتضمن مراقبة الحالة تتبع المعايير مثل الاهتزاز، درجة الحرارة والرطوبة للحصول على رؤى حول تشغيل المعدات. من خلال دمج ممارسات الصيانة القائمة على الحالة، يمكن للمصنعين تحسين كفاءة المعدات الشاملة (OEE) بشكل كبير عن طريق تقليل العيوب غير المتوقعة والوقوف. يختلف هذا النهج الوقائي بشكل حاد عن الأساليب التفاعلية التقليدية، حيث يتم تحويل البيانات التاريخية إلى استراتيجيات قابلة للتنفيذ، مما يُحسن أداء المعدات.
تكامل إنترنت الأشياء لمراقبة المعدات في الوقت الفعلي
تُعتبر تقنيات إنترنت الأشياء محورية في تمكين مراقبة المعدات في الوقت الفعلي وتقديم بيانات حيوية حول أداء الماكينات ومؤشرات صحتها. يستخدم استشعار الماكينات المدمجة تسهيل جمع البيانات المستمر، والذي يمكن أن يكون حاسمًا لاتخاذ قرارات ذكية بشأن جداول الصيانة. يدعم هذا النهج رؤى صناعية تشير إلى أن تنفيذ حلول إنترنت الأشياء يمكن أن يقلل من التوقف غير المخطط له بنسبة تصل إلى 30%. كما أن جمع البيانات في الوقت الفعلي يمكّن المنظمات من اتخاذ تدخلات استباقية، مما يقلل من الانقطاعات في الإنتاج ويعزز استمرارية العمليات.
تعلم الآلة في أنظمة التنبؤ بالفشل
تقدم خوارزميات التعلم الآلي مزايا كبيرة من خلال تحليل البيانات التاريخية لاكتشاف الأنماط التي تشير إلى احتمالية فشل المعدات. هذه القدرة تجعل المؤسسات تنتقل من استراتيجيات الصيانة التفاعلية إلى الاستباقية باستخدام التحليلات التنبؤية لتحسين تخصيص الموارد. وفقًا للأبحاث من خبراء تقنيين رئيسيين، يمكن للشركات التي تستفيد من التعلم الآلي للصيانة التنبؤية تقليل تكاليف الصيانة بنسبة حوالي 25%. من خلال التنبؤ بالمشاكل قبل أن تتفاقم، يمكن للمؤسسات تحسين عمليات الصيانة وزيادة كفاءتها وموثوقيتها العامة في بيئات الإنتاج. دمج التعلم الآلي بشكل فعال يطيل عمر الماكينات بالإضافة إلى تعزيز الإنتاجية والأمان.
تحسين كفاءة تصنيع الأحذية
تقليل التوقف غير المخطط له في معالجة الجلود
فهم ومعالجة الأسباب الجذرية لتعطل التشغيل غير المخطط له في معالجة الجلود يمكن أن يعزز بشكل كبير كفاءة الإنتاج. تحليل البيانات من الحوادث السابقة يساعد في تطوير استراتيجيات مستهدفة لتقليل مثل هذه الاضطرابات. جداول الصيانة الدورية، عندما يتم تنسيقها مع التحليل التنبؤي، تلعب دورًا حاسمًا في تقليل الانقطاعات غير المتوقعة. هذا النهج الاستباقي يضمن أن تكون الآلات في حالة مثلى، مما يقلل من وقت التعطل. تشير الأدلة إلى أن المنظمات التي تركز على أنشطة الصيانة يمكنها تحقيق إنتاجية أعلى بنسبة تصل إلى 15٪، مما يؤكد الأهمية الاستراتيجية لثقافة الصيانة في العمليات الصناعية.
LSI Technologies: الدقة في عمليات خياطة الأحذية
التكامل بين تقنيات LSI المتقدمة وعمليات خياطة الأحذية يعزز الدقة والكفاءة، مما يؤدي إلى منتجات ذات جودة أعلى. تلعب ماكينات الخياطة الحديثة المجهزة بتحكم أوتوماتيكي في الخياطة دورًا محوريًا لتحقيق دقة عالية، وتقليل الأخطاء البشرية، وتسريع عملية التصنيع. وفقًا لدراسات الحالة، يمكن أن يؤدي تنفيذ تقنيات الدقة إلى تقليل هدر المواد بنسبة 20٪. مثل هذه الادخارات لا تقلل فقط من التكاليف، بل تسهم أيضًا في ممارسات تصنيع مستدامة، مما يجعل الدقة عاملًا رئيسيًا للمنافع الاقتصادية والبيئية في إنتاج الأحذية.
دراسة حالة: تحسين كفاءة استخدام المعدات في صناعة السيارات
يمكن أن تستفيد صناعة الأحذية بشكل كبير من الدروس المستفادة من تحسينات صناعة السيارات في فعالية المعدات العامة (OEE). من خلال تبني مبادئ التصنيع النحيف واستخدام التحليلات المتقدمة، شهدت شركات السيارات تحولاً ملحوظاً في كفاءة إنتاجها. تكشف البيانات الحديثة أن استراتيجيات OEE الفعالة رفعت الإنتاج بنسبة تزيد عن 30%. يوضح هذا النجاح قوة ممارسات الكفاءة المنظمة مع اتخاذ قرارات مدفوعة بالبيانات، مما يقدم نموذجاً لشركات تصنيع الأحذية التي تسعى إلى تحسين أدائها التشغيلي والحفاظ على حافة تنافسية في السوق.
حلول الصيانة التنبؤية جاهزة من شركة تينغ هونغ للماكينات
TH-739B: ماكينة تثبيت الرأس بذاكرة الكمبيوتر ذات القواصر السبعة
النظام الكهربائي TH-739B تم تصميم النموذج لتعزيز الدقة في مهام تشكيل أطراف الأحذية من خلال التحكم بذاكرة الكمبيوتر المتقدمة. هذه التقنية المبتكرة تضمن تكراراً دقيقاً، وهو أمر حيوي لتلبية متطلبات صناعة الأحذية الصارمة. تساعد الميزات الآلية للنموذج TH-739B في تقليل أوقات الدورة، مما يزيد بشكل كبير من كفاءة الإنتاج. تشير بيانات المبيعات إلى أن مستخدمي TH-739B حققوا خفض بنسبة 15% في تكاليف الإنتاج، مما يؤكد كفاءته في تحسين عمليات التصنيع.
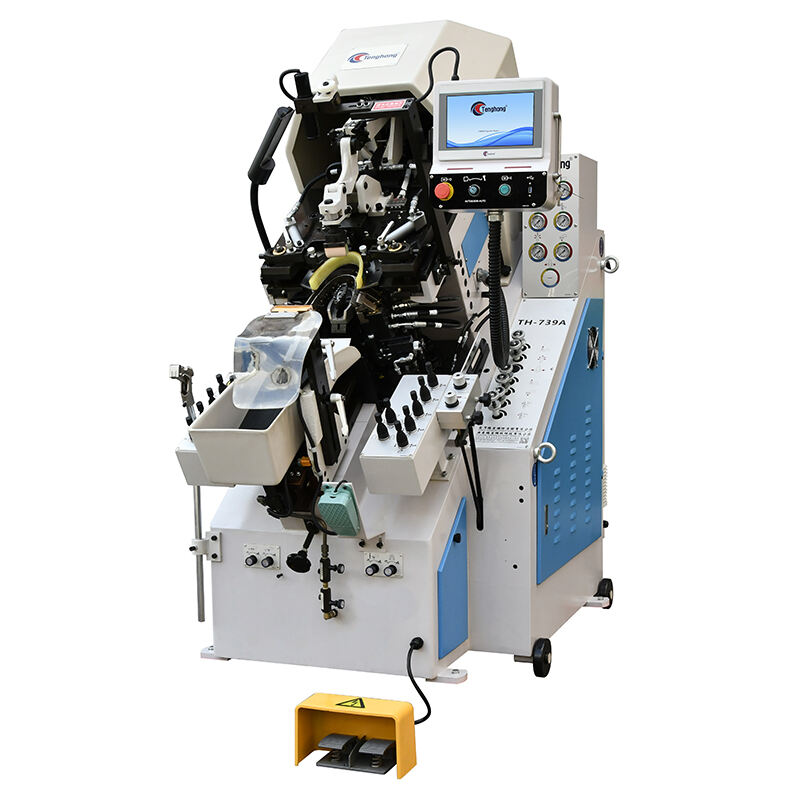
TH-747A: نظام آلي بـ9 ملاقط مع تشخيص الأخطاء
النظام الكهربائي TH-747A مجهز بأدوات تشخيص الأخطاء، مما يجعل حل المشكلات في الوقت الفعلي أثناء الإنتاج سلسًا. يسمح هذا النظام للمشغلين بتحديد وتصحيح المشكلات بسرعة، مع الحفاظ على معايير الجودة العالية التي تعتبر ضرورية للتصنيع التنافسي. تُشيد شهادات المستخدمين بالجهاز TH-747A لتحسينه الملحوظ لكفاءة الإنتاج، مما يسمح للمصنعين بالحفاظ على معايير عالية دون التضحية بالسرعة.
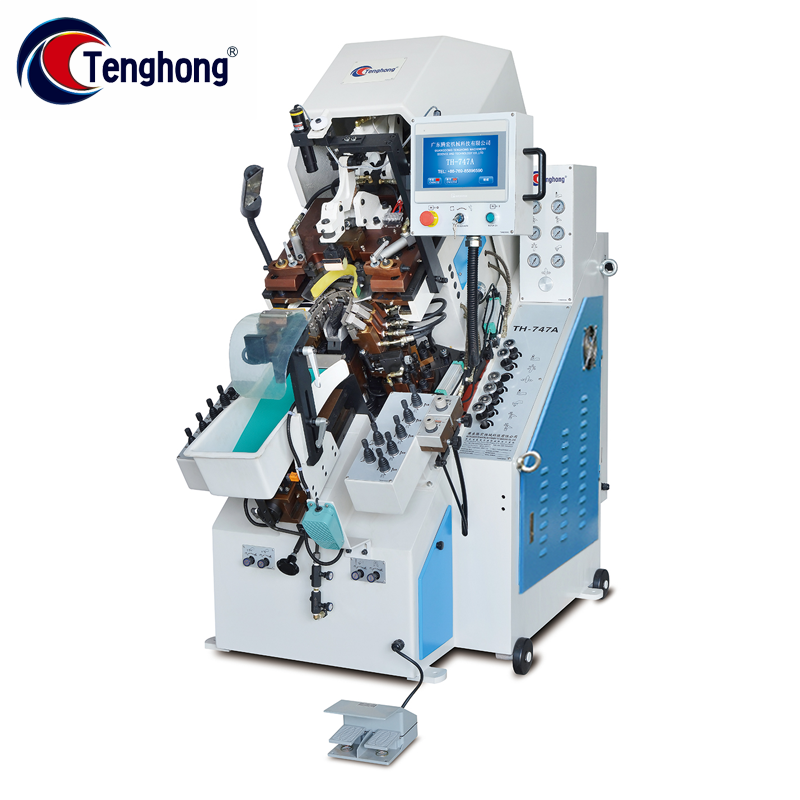
TH-747MA: جهاز التصاق الأحذية مع تحكم ذكي في العملية
النظام الكهربائي TH-747MA تحتوي على تحكمات عملية ذكية تُحسّن من اتساق المادة اللاصقة، وهي أمر حيوي لضمان سلامة منتجات الأحذية. هذه التحكمات الذكية تبسط العمليات وتقلل من هدر المواد، مما يضمن بقاء جودة المنتج دون تنازل. تشير المعايير الصناعية إلى أن استخدام الآلات الذكية مثل TH-747MA يمكن أن يزيد من قوة المادة اللاصقة بنسبة 10%، مما يعزز كلاً من متانة المنتج وكفاءة التصنيع.
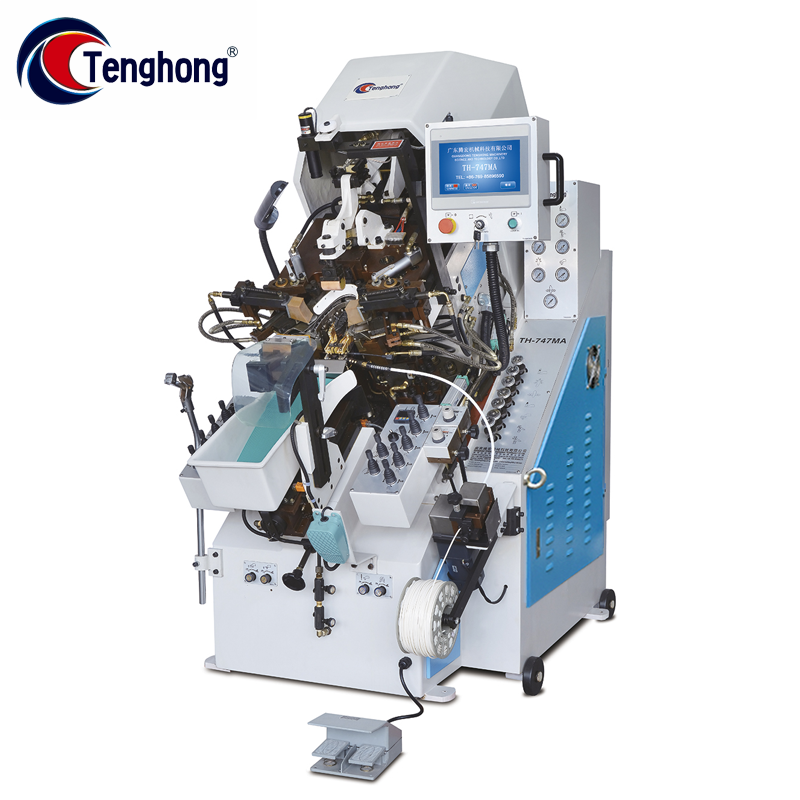
تنفيذ البروتوكولات لخطوط معالجة الجلود
تخصيص استراتيجيات تنبؤية لعمليات تشغيل ماكينات القص
تخصيص استراتيجيات الصيانة التنبؤية لعمليات تشغيل ماكينات الضغط يمكن أن يعزز الإنتاجية بشكل كبير في صناعة معالجة الجلود. من خلال تحديد التحديات التشغيلية الفريدة، يمكن للشركات تكييف هذه الاستراتيجيات لتلبية احتياجات الإنتاج المحددة بكفاءة. على سبيل المثال، قد تتضمن استراتيجية تنبؤية جمع بيانات حول أنماط تآكل الآلة، مما يساعد في جدولة الصيانة في الوقت المناسب. تشير التقارير إلى أن تنفيذ خطط صيانة مخصصة أدى إلى زيادة بنسبة 25٪ في وقت تشغيل الآلات، مما يظهر إمكاناتها لتحسين الكفاءة التشغيلية بشكل كبير.
دورة تحسين مستمرة مدفوعة بالبيانات
إنشاء مناهج تعتمد على البيانات يعزز ثقافة التحسين المستمر داخل خطوط معالجة الجلود. تعتبر تحليل بيانات الأداء بشكل منتظم أمرًا حيويًا، حيث يساعد في تحديد المناطق التي تحتاج إلى تحسين، مما يضمن ممارسات تصنيع مستدامة. تشير الدراسات الطولية إلى فوائد هذا النهج، حيث تظهر أن المنظمات التي تتبنى التحسين المستمر تحقق مكاسب تصل إلى 20% في كفاءة العمليات. من خلال استخدام هذه الاستراتيجية، يمكن لخطوط معالجة الجلود تحسين تخصيص الموارد بينما تحتفظ بمعايير الإنتاج المرتفعة.
تكامل تحليلات قاطع شرائح الجلد
تتيح دمج التحليلات في عمليات قطع شرائح الجلد تحسين دقة القطع واستخدام المواد. من خلال جمع البيانات أثناء عملية القطع، يمكن للمشغلين إجراء تعديلات مدروسة تُحسن جودة الإنتاج وتقلل من الهدر. أثبتت هذه المبادرات التي تعتمد على التحليلات أنها تؤدي إلى تقليل النفايات بنسبة حوالي 15٪ في الإنتاج. من خلال الاستفادة من مثل هذه التقنيات، يمكن لخطوط معالجة الجلد تحسين العمليات، تقليل التكاليف، وتحقيق جودة منتجات متسقة، مما يساهم في فعالية التصنيع بشكل عام.
بشكل عام، تنفيذ هذه البروتوكولات عبر مراحل مختلفة من خط معالجة الجلد لا يعزز الكفاءة فقط، بل يشجع أيضًا نهجًا مستدامًا ومدعومًا بالبيانات للتصنيع. من خلال الاستفادة من استراتيجيات التنبؤ، والتحسينات المستندة إلى البيانات، والتحليلات، يمكن للشركات ضمان أن تكون عملياتها كفوءة وتنافسية.