Understanding the Role of Sole Attaching Machines in Footwear Manufacturing
The Importance of Sole Attaching Machines in Footwear Manufacturing
Sole attaching machines play a pivotal role in the footwear manufacturing process by bonding various shoe components, such as soles, to the upper parts. This is a critical step, ensuring that the footwear maintains its durability and structural integrity. The machines streamline bonding based on the shoe construction method, enhancing the quality and efficiency of the production process. These machines utilize different approaches, such as cementing, vulcanization, and injection molding, to ensure that the sole is securely attached to the upper, catering to various styles and types of shoes.
Key features of sole attaching machines include speed, precision, and diverse adhesive applications, which have a significant impact on footwear quality and durability. The speed at which these machines operate allows for higher production rates, reducing manual labor and increasing overall efficiency. Precision via automation ensures that adhesives are applied consistently, leading to enhanced product quality and uniformity. Moreover, the ability to handle different adhesive types enables manufacturers to produce diverse shoe styles, from casual shoes to specialized footwear, with optimal durability and finish.
Benefits of Sole Attaching Machines in Footwear Production
Sole attaching machines have revolutionized the footwear industry by significantly enhancing production efficiency. These machines automate the bonding process, which drastically reduces the manual labor hours required in footwear manufacturing. For instance, a sole attaching machine can handle the bonding task with incredible speed and precision, completing in minutes what would take a manual worker hours. This automation boosts output rates, allowing manufacturers to increase their production capacity without the need to expand the workforce. The automation not only accelerates the production process but also optimizes resource allocation and reduces overhead costs.
Moreover, sole attaching machines greatly improve the quality and consistency of footwear production. By employing precise mechanisms and universally-standardized settings, these machines minimize defects in shoes. According to industry experts, the reliability of machinery results in a reduced defect rate in footwear, contributing to a significant improvement in product quality. A study found that automated sole attaching processes decrease defect rates by up to 30%, ensuring uniformity and heightening consumer satisfaction. This level of consistency is challenging to achieve with manual production, emphasizing the critical role machines play in achieving high standards across every batch of footwear produced.
Types of Sole Attaching Machines
Several types of sole attaching machines play crucial roles in footwear production, with each type offering distinct advantages suited to specific production needs. Hydraulic sole attaching machines operate using a full hydraulic system, providing significant power advantages ideal for high-volume production environments. Their robust pressure capabilities ensure a firm fit for various shoe types, including wall-covered sports and casual shoes. These machines also offer enhanced operational speed and reliability, allowing businesses to maximize output while maintaining quality.
When it comes to automation, automatic and manual sole attaching machines offer varying levels of ease and precision. Automatic machines streamline the bonding process, reducing the necessity for manual intervention, which can significantly enhance productivity. However, they may require a higher initial investment and specialized training. In contrast, manual machines offer greater control on projects with more artisanal requirements but may result in slower production speeds. Businesses must weigh these pros and cons to select the most suitable option based on their production scale and quality expectations. This choice can directly impact the efficiency and effectiveness of their operations.
Choosing the Right Sole Attaching Machine for Your Footwear Business
Selecting the right sole attaching machine is crucial for any footwear business aiming to enhance productivity and maintain quality. Key factors to consider include:
- Budget: Assess the financial constraints and evaluate the costs of different machines to ensure you get the best value without overspending.
- Machine Capabilities: Determine the types of shoes you plan to produce—like sports shoes, casual wear, or boots—and ensure the machine can handle these efficiently.
- Maintenance Needs: Consider the ease and frequency of maintenance, which can impact operational costs and downtime.
- Skill Level Required: Analyze whether your workforce possesses the required skills or if additional training is necessary, especially if you are considering advanced machinery like shoe sewing machines or leather clicker presses.
Matching these factors with your production goals can lead to a more streamlined manufacturing process, ultimately impacting your bottom line.
Understanding your production needs is equally vital. Businesses must assess their output requirements in alignment with market demands. For example, if the demand for custom sneakers is rising, consider a machine with the flexibility to switch between different materials and styles rapidly. Real-world examples include the rise of on-demand production in tech-savvy factories, allowing businesses to quickly adapt to trends and consumer needs. By understanding whether a manual machine suffices or advanced automation is necessary, you can align your choice with your specific production requirements, thus enhancing efficiency and profitability.
Product Overview: Leading Sole Attaching Machines in the Market
When it comes to leading sole attaching machines, the TH-7900 3D Shoes Vamp Hot&Cold Molding Machine stands out for its versatility and precision. This machine is engineered to handle various shoe types, including men's and women's footwear. Known for its accuracy in molding without double cutting or leaving any knife marks, the TH-7900 offers a perfect shaping effect and shortens shaping time significantly. A testament to its effectiveness, customers have reported increased production efficiency and superior shaping outcomes. The machine supports precise positioning, making it ideal for sophisticated synthetic materials and leather.
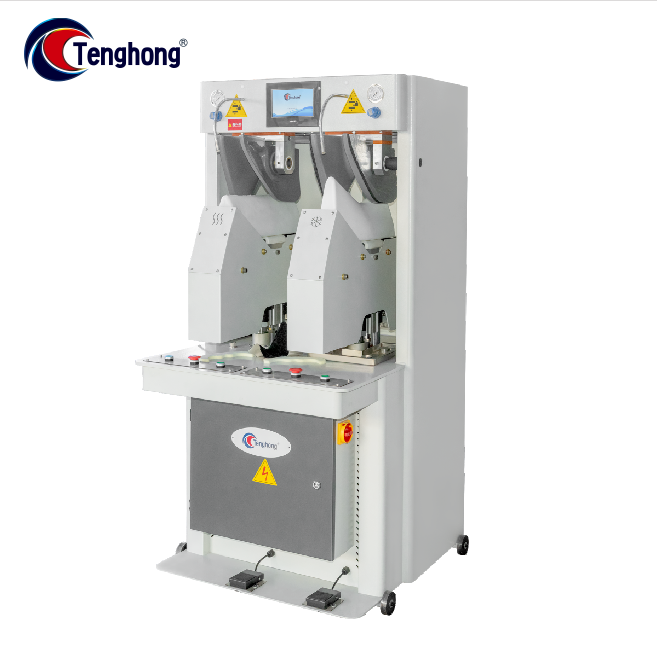
For specialized stitch-down shoe designs, the TH-319 Two Cold And Two Hot Counter Moulding Machine delivers excellent performance. It features dual cooling and heating systems, enabling enhanced mold customization for superior shape effects. The machine's design includes adjustable components for seamless vamp and last jointing, which is critical in maintaining shoe integrity during molding. Its environmentally friendly cooling system reaching -30°C and precise electronic heating up to 200°C make it suitable for exacting shoe construction requirements.
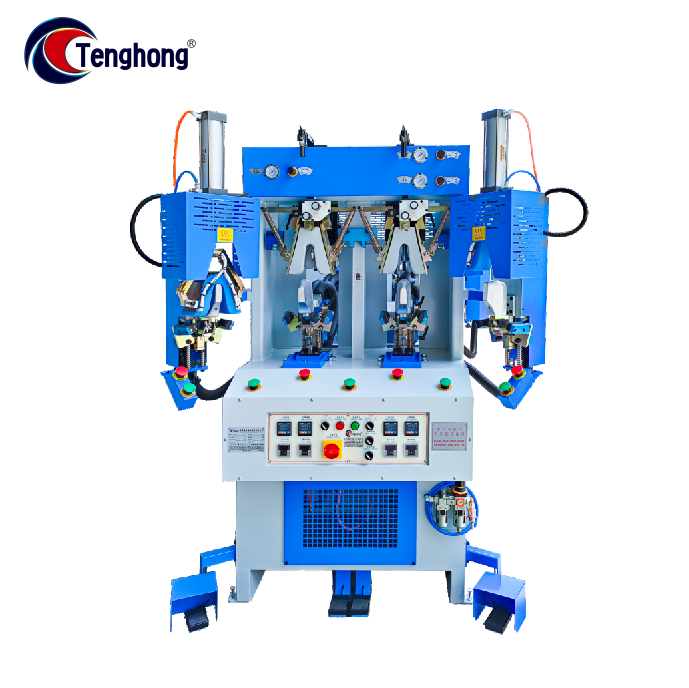
Lastly, the Four Column Hydraulic Vertical-type Leather Measuring Cutting Machine For Plastic EVA Leather Shoes Making Tenghong TH-109 offers remarkable efficiency in cutting materials needed for sole attaching. This machine is particularly beneficial in shoe factories where precise measurement and material preparation are critical. Equipped with advanced infra-red digital scanning, it enhances measuring accuracy and is adaptable for use in different leather product factories. The TH-109's user-friendly design and high reputation make it a valuable asset for efficient and precision-driven operations.
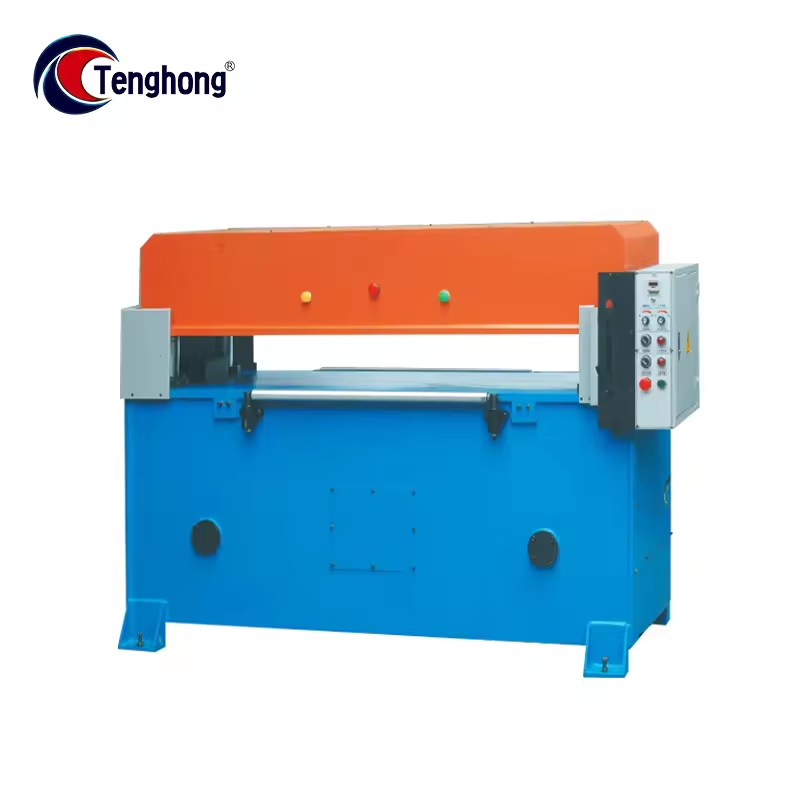
Conclusion: Embracing Technology in Footwear Manufacturing
The future of sole attaching machines is marked by advancements in AI and automation technologies that promise to enhance productivity radically. These emerging technologies are projected to improve precision, reduce production time, and allow for greater customization in footwear manufacturing. By integrating AI-driven processes, manufacturers can potentially achieve higher efficiency and adaptability, meeting the increasing demand for personalized products.
Innovation is crucial for staying competitive in the rapidly evolving footwear industry. Manufacturers must continuously adopt cutting-edge technologies to remain relevant and efficient. Embracing new machinery and production techniques enables companies to improve quality, reduce costs, and respond swiftly to market demands. This proactive approach to technology adoption not only ensures competitive advantage but also sets the foundation for sustainable growth in the industry.